Hartstoffbeschichtungen verlängern die Lebensdauer von Sinterbrecherkomponenten und sparen Energie und CO2
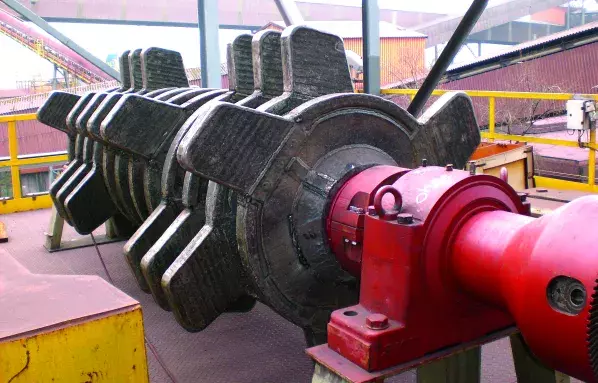
Der Sinterbrecher spielt eine entscheidende Rolle im Stahlwerk und ist oft der Schlüssel zur Rentabilität. Daher ist ein proaktiver Ansatz bei der Wartung unerlässlich. Martin Kirchgassner, Chief Technology Officer (CTO) von Castolin Eutectic, erklärt, wie die Aufpanzerungstechnologie Brecherkomponenten, die starkem Verschleiß ausgesetzt sind, widerstandsfähiger macht.
Als Maschinen, die stark abrasiven Sinter in Stücke geeigneter Größe für die Beschickung des Hochofens zerkleinern, sind Sinterbrecher einem extremen Verschleiß ausgesetzt. Da Sinter heiß, hart und abrasiv ist, stellt er eine große Herausforderung für die Handhabung dar.
Der Verschleiß tritt vor allem in zwei Bereichen auf: an den Rostbalken und an den Zähnen des Rotors. Aber auch die Rutsche, über die das Material in die Maschine gelangt, kann in Mitleidenschaft gezogen werden, wenn der Sinter durch sie hindurchfällt, ebenso wie die Siebe, die das Material sortieren, um den Feinanteil herauszufiltern, damit er als Ausgangsmaterial für die Herstellung von mehr Sinter verwendet werden kann.
Die Rostbalken unterliegen dem größten Verschleiß. Sie bestehen aus großen rechteckigen Stahlstäben, die wie ein Kamm parallel angeordnet sind, wobei jeder Stab 100 mm breit und bis zu 3 m lang ist. Wenn der Sinter in den Brecher gegeben wird, wird er von den Zähnen des sich drehenden Rotors erfasst. Diese befördern und zertrümmern den Sinter in die Stäbe und setzen sie einer intensiven mechanischen Schlagbelastung aus, die eine Wartung alle sechs Wochen erforderlich machen kann.
Dieser Vorgang führt auch zu einer starken Abnutzung der Rotorkomponenten. Dazu gehören in der Regel zwei bis vier Zähne, die den Sinter aufnehmen und bearbeiten, sowie die Scheiben, auf denen die Zähne montiert sind. Normalerweise halten die Zähne weniger als ein Jahr.
Herkömmliche Möglichkeiten zur Bekämpfung des Verschleißes
Um den Verschleiß zu verringern und damit die Lebensdauer eines Brechers zu verlängern, stehen dem Betreiber verschiedene Möglichkeiten zur Verfügung. Dadurch bleibt die Leistung der Anlage erhalten, was zu einer effizienteren Produktion führt. Traditionell haben die Betreiber mehrere Möglichkeiten, dies zu erreichen.
Die erste besteht darin, den hohen Verschleiß und die regelmäßigen Stillstände, die für die Überholung der Komponenten und die Behebung des Verschleißes erforderlich sind, einfach zu akzeptieren. In diesem Fall werden Rostbalken aus Baustahl mit hoher Verschleißhärte verwendet, z. B. aus den Legierungen S275 oder S355. Alternativ wird für die Rotorzähne oft Manganstahl verwendet. Dies kann für einen Brecher mit relativ geringer Verschleißrate geeignet sein.
An Standorten mit intensiverem Verschleiß aufgrund höherer Temperaturen, der Belastung und der mechanischen Konstruktion müssen die Betreiber jedoch Maßnahmen ergreifen, um eine höhere Verschleißfestigkeit zu erreichen. Wenn die Anforderungen steigen, können die Betreiber den Einbau von verschleißfesten Auskleidungen oder Einsätzen, das Aufbringen von verschleißfesten Aufpanzerungen, die Verwendung von Verschleißplatten und die Integration von Wasserkühlung in die Rostbalken in Betracht ziehen.
Auskleidungen oder Einsätze werden in der Regel aus Matrixmaterialien hergestellt, die Hartmetalle enthalten. Mit zunehmendem Verschleiß können diese jedoch immer noch schnell verschleißen.
Daher besteht die nächste mögliche Taktik darin, die Bereiche mit hohem Verschleiß mit einer Panzerbeschichtung zu versehen. Beim Rotor sind dies in der Regel die Außenkanten der Zähne und der Scheibenkörper des Rotors, wohingegen die Rostbalken eine 10-15 mm dicke verschleißfeste Schicht erfordern, die auf die Oberseite der Stäbe geschweißt wird, sowie 5-8 mm an den Kanten.
Damit werden die angestrebten Vorteile möglicherweise immer noch nicht erreicht. So bietet die Beschichtung auf den Rotoren möglicherweise keinen ausreichenden Schutz gegenüber dem Grundmaterial, das sich manchmal zuerst abnutzt. Außerdem haben Aufpanzerungen in der Regel einen geringeren Wärmeübergangskoeffizienten als Baustahl.
Daher kann das Aufbringen einer dicken Beschichtung auf Rostbalken die unbeabsichtigte Folge haben, dass sich ein Wärmestau bildet. Dies wiederum kann zu einer Verringerung der Verschleißfestigkeit führen, so dass sich Risse in der dicken Schicht bilden und ausbreiten können, was wiederum zu Abplatzungen führt, bei denen Fragmente der äußeren Panzerschicht vorzeitig verloren gehen.
Leistungsstarke Castolin Eutectic-Lösung
Die Herausforderung besteht darin, dass es für alle diese Lösungen eine Grenze gibt. Um die Verfügbarkeit ihrer Sinterbrecher zu schützen, entscheiden sich viele Werke daher für eine Hochleistungspanzerung, die genau auf die auftretenden Verschleißraten zugeschnitten ist.
Der Einsatz einer solchen Lösung kann die Lebensdauer der wichtigsten Komponenten eines Brechers um das Dreifache verlängern. Dadurch werden die Wartungsintervalle erheblich verlängert und die Häufigkeit von Wartungsausfällen reduziert, während die Produktivität der gesamten Anlage erhalten bleibt.
Der Castolin Eutectic-Ansatz verwendet Legierungen mit extrem hoher Verschleißfestigkeit, die Temperaturen von 400 °C und mehr standhalten können. Der Schlüssel zum Erfolg ist das Fachwissen bei der Auswahl des Materials und die Anwendung einer Applikationstechnik, die Ankerpunkte im Stahlbauteil nutzt, sowie ein spezielles Schweißmuster, das die Haltbarkeit einer relativ dünnen Beschichtung maximiert.
Einsparung von Energie und Emissionen
Während das Hauptziel einer Auftragsschweißung darin besteht, die Lebensdauer von Brecherkomponenten zu verlängern, behalten die Komponenten ihre ursprüngliche Geometrie länger bei. Daraus ergibt sich der sekundäre Vorteil, dass die Maschine bei der vorgegebenen Energieeffizienz länger Sinter zerkleinern kann. Wenn die Komponenten hingegen verschlissen und verrundet sind, wird mehr Energie benötigt, um die gleichen Brechergebnisse zu erzielen.
Darüber hinaus spart die Verlängerung der Lebensdauer von Stahlteilen die Energie, die sonst für die Herstellung neuer Brecherzähne oder - Rostbalken zum Ersatz verschlissener Teile erforderlich wäre.
Daher kann eine Auftragsschweißbeschichtung eine Taktik zur Senkung des Energieverbrauchs und der CO2-Emissionen sein und wertvolle Betriebszeit und Mühleneffizienz schützen.
Diese Art von fortschrittlichem Beschichtungssystem wurde 2013 entwickelt und ist inzwischen in neun Stahlwerken in ganz Europa im Einsatz, entweder als Komplettlösung oder als Testkomponenten. An einem dieser Standorte wurde der Ansatz im Vergleich zu einer Beschichtungslösung für verschiedene Zähne auf derselben Rotorscheibe getestet.
Bei der an diesem Standort traditionell eingesetzten Lösung war die Auskleidung nach 10 Monaten Betrieb und einer Produktion von 2,4 Millionen Tonnen Sinter in der Regel vollständig verschlissen und musste ersetzt werden.
Kalkulation des Business Case
Die Kosten für eine Hochleistungslösung müssen höher sein, da sie qualitativ hochwertige Rohstoffe sowie fachkundige Techniker für die Spezifizierung und Anbringung der Materialien erfordert. Es liegt jedoch auf der Hand, dass sie eine höhere Verfügbarkeit und geringere Ausfallzeiten ermöglichen, was zu finanziellen Einsparungen führt. Diese können für Werke, in denen die Sinteranlage ein geschäftskritischer Prozessschritt ist, der die Gesamtproduktion beeinflusst, erheblich sein.
Die Berechnung der Investitionskosten für eine Hochleistungspanzerung ist eine komplexe Berechnung. Sie ist von Standort zu Standort unterschiedlich und hängt von der Auslastung der Anlage, von der Frage, ob genügend Sinter vorrätig ist, um Ausfälle zu überbrücken, sowie von den Kosten und der Verfügbarkeit alternativer Einsatzstoffe für den Ofen ab.
Es ist wichtig, ein Testmuster zu erhalten, das mit der Hochleistungspanzerung behandelt wurde, und es mit der vorhandenen Lösung zu vergleichen, um die vergleichbare Leistung vollständig zu verstehen und zu bewerten. Die erforderlichen Wartungsintervalle sowie die Arbeits- und Ersatzteilkosten, die vom Ausmaß der Abnutzung, der Größe der Maschine und der Art der erforderlichen Wartung abhängen, werden in den Business Case einbezogen.
Steigerung der Produktionseffizienz
Der Sinterbrecher ist ein wichtiger Ausrüstungsgegenstand, der einem hohen Verschleiß unterliegt und die gesamte Produktionsleistung einer Mühle beeinflussen kann. Daher kann es sich lohnen, in Hochleistungs-Auftragsschichten auf Schlüsselkomponenten wie Rostbalken und Zähne zu investieren, die dem Verschleiß standhalten und ihre Form länger beibehalten.
Selbst eine bescheidene Verbesserung der Lebensdauer hat das Potenzial, den Energieverbrauch und die CO2-Emissionen zu senken, da die Komponenten ihre ursprüngliche Form beibehalten. Darüber hinaus können erhebliche Kosteneinsparungen erzielt werden, da weniger Wartungsarbeiten anfallen und die Betriebszeit verlängert wird.