Improving Hydropower Plant Longevity through Cavitation and Erosion Mitigation
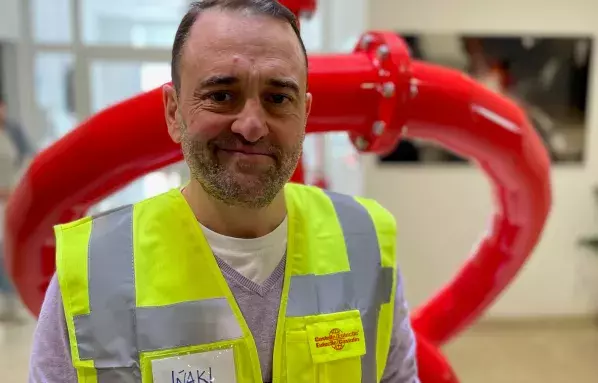
Erosion and cavitation are significant wear mechanisms that can drastically shorten the operational lifespan of machinery components in hydropower plants. The application of ultra-hard wear-resistant coatings is essential to combat these challenges, although each site presents unique conditions requiring tailored solutions. In this article, Inaki Ezpeleta, an applications engineer at Castolin Eutectic, explores how customized wear coatings can effectively resist erosion and cavitation, ensuring sustained reliability and availability of hydropower equipment.
When discussing mechanical equipment wear, cavitation and erosion emerge as critical concerns. Cavitation occurs due to pressure changes in water flow, leading to the formation and collapse of vapor bubbles behind impeller blades. This phenomenon induces shock waves that cause pitting, cracking, and eventual failure of the impeller surfaces. On the other hand, erosion results from the impact of abrasive sand particles in water, gradually wearing down components over time.
Hydraulic machines of varying types, sizes, and ages are susceptible to cavitation and erosion. While complete elimination of these wear mechanisms is impractical, periodic repairs using materials with high surface hardness and toughness can restore components to their original efficiency and extend their service life.
The impact of cavitation and erosion varies at each hydropower site, influenced by factors such as water pressure, flow rate, sediment composition, and operating conditions. To address these challenges effectively, a diverse array of coatings is available. These coatings are specifically designed to repair and protect turbines (e.g., Francis, Kaplan, propeller, bulb), draft tubes, impellers, pumps, valves, and wicket gates. Techniques including HVOF (High-Velocity Oxygen Fuel), arc spraying, welding, and cold polymeric coatings are employed to apply wear-resistant alloys tailored to the unique wear patterns of each site.
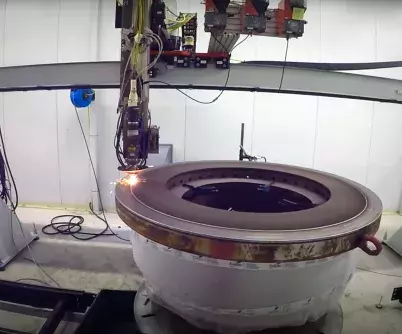
Case Study: CaviTec
A notable example is the development of CaviTec, a cavitation-resistant alloy pioneered by Hydro-Quebec to combat erosion on turbine runners across its extensive hydropower fleet. This stainless-steel alloy graded such as 308 or 309, fortified with chromium, cobalt, silicon, and manganese, surpasses traditional grades by lasting up to six times longer under rigorous testing conditions.
Continual advancements enhance the precision and durability of these alloys. Innovations like pulse welding and optimized application parameters minimize porosity and improve coating quality and longevity. These developments ensure that components maintain optimal performance over extended operational periods.
Repair Techniques
When cavitation causes significant material loss, welding repairs become essential. Techniques such as arc-air or plasma gouging are used to remove damaged material before grinding and welding new layers onto surfaces. A base layer of stainless steel, followed by an overlay of CaviTec, ensures optimal thickness and performance, exemplified in the repair of Francis pump turbines in Austria.
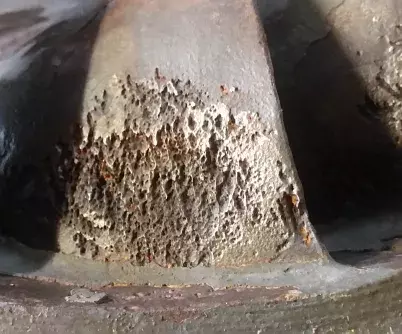
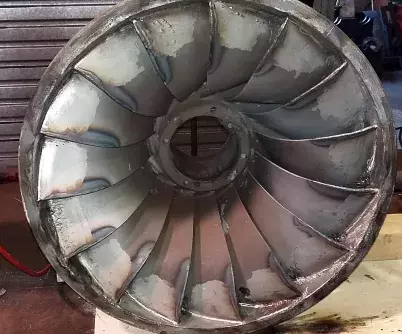
Considerations in Thermal Spraying
In industries where erosion poses a significant threat, thermal spraying offers a vital solution. This method allows for the application of thin, dense coatings that are crucial for maintaining operational efficiency in machinery subjected to abrasive environments over time.
Long-term performance and repairability are critical factors when selecting thermal spraying techniques. The bond strength of coatings, a key metric, influences the choice between HVOF and arc spray. Both methods are renowned for their robust bond strength, ensuring durability and reliability for both new applications and repairs. The selection of the appropriate technique depends on the specific requirements of the coating.
HVOF is particularly effective for applying coatings such as tungsten carbide cobalt chromium (WC/Co/Cr) at high speeds. This method not only offers superior erosion resistance but also combats cavitation effectively. By utilizing high velocity rather than high temperatures, HVOF minimizes adverse thermal effects on the underlying component, thereby preserving its integrity.
The versatility of HVOF allows for spot applications or complete component coverage, facilitating on-site repairs with ease.
Alternatively, amorphous materials containing chromium, boron, and silicon provide another option for erosion resistance. Applied using arc spray, these materials create dense coatings that adhere well to steel substrates. While more economical than HVOF, they do not achieve the extreme surface hardness of tungsten carbide.
Case Study: Addressing Erosion Challenges
At a hydropower plant in Austria, erosion due to sand-laden water posed a significant challenge for a 6 MW high-pressure pump turbine. The abrasive particles, measuring 0.5 mm and larger, caused erosion between shaft seals and runners, leading to varying service lives of 3000 to 6000 hours. In severe cases, rapid wear necessitated immediate repairs to prevent excessive leakage.
As a proactive measure, technicians applied a 0.3 mm HVOF coating, extending maintenance intervals significantly. Inspection after 2200 operational hours revealed minimal wear, demonstrating the efficacy of HVOF in enhancing equipment longevity.
Laser Cladding for Enhanced Durability
Laser cladding represents another innovative approach for rebuilding and resizing components. This technique utilizes a laser to heat metallic powder or wire on the workpiece's surface, creating a robust metallurgical bond. Known for its precision and rapid heating capabilities, laser cladding offers flexibility in choosing and grading coatings, accommodating diverse operational needs.
In one notable application in Norway, a six-ton component suffering from severe wear underwent extensive refurbishment using a 6 kW laser cladding machine. This approach not only restored the component quickly but also minimized environmental impact by utilizing emission-free Nordic electricity, contrasting with traditional welding repairs that generate harmful emissions.
Ceramic Surfacing Polymers for Versatile Maintenance
Ceramic surface polymers, branded as MeCaTec, blend ceramic strength with polymer flexibility, making them ideal for combating cavitation and erosion. Available as a two-part compound, these polymers are applied on-site using trowels, brushes, or sprays. They serve both corrective and preventive maintenance purposes, ensuring prolonged component lifespan and operational efficiency.
For instance, at a hydropower plant, a perforated water supply pipe on a cast iron storage tank was swiftly restored using ceramic polymer. Given the complexity of welding or thermal repairs for cast iron, this compound efficiently repaired and sealed perforations, promptly returning the component to service.
Conclusion
Effective management of erosion challenges in hydropower components demands a strategic selection of materials and techniques. By leveraging advanced thermal spraying, laser cladding, and ceramic surface polymers, industries can enhance equipment durability, minimize downtime, and optimize maintenance costs. For tailored solutions and further inquiries, visit www.castolin.com/contact.