Castolin Eutectic brings wearplate manufacturing and vertical roll mill refurbishment to South Africa
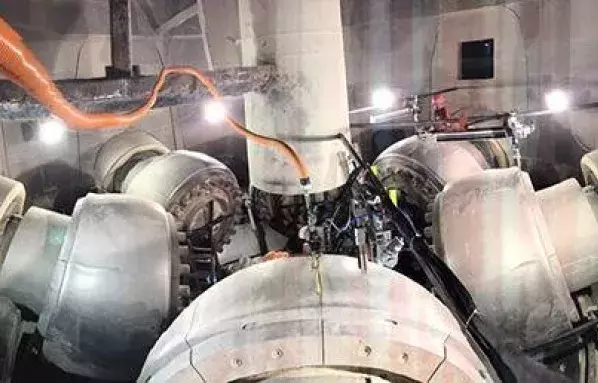
Having signed up as a Castolin Eutectic licensee, Hlakani Engineering is currently installing and commissioning our technology to bring the Castolin Eutectic refurbishment and life-extension offerings into South Africa and Southern Africa. Hlakani is a black woman-owned company with a B-BBEE Level 2 score and this agreement enables us to tender for and deliver turn-key refurbishment projects to equipment operators across the region.
Hlakani intends to introduce a comprehensive range of Castolin Eutectic services, including:
- Vertical rolling mill (VRM) coating technology for the weld refurbishment of worn cement and coal mill rollers and tables to original profiles.
- The manufacture and distribution of CastoDur Diamond Weld overlay plate (CDP).
- CastoTube technology for internally coated mild steel tubes and pipes.
- Boiler coating using thermal spray technology – Whertec.
- Wear resistant ceramic tiles – CastoCeram.
- Anti-wear polymer coating services and repair of all metals, including difficult-to-weld metals such as Ni-Hard castings – Mecatec.
VRM refurbishment
Globally, Castolin Eutectic has developed state-of-the-art VRM roller and table welding technology for in-situ welding with advance welding control systems. Simultaneously using up six welding heads, deposition rates can be maximised to reduce mill outage to an absolute minimum. By taking repair solutions to site, time and handling costs for the removal and re-installation of mill table and rollers are also avoided.
Hlakani’s top priority is VRM technology transfer, which will start from March/April 2019. “VRM repairs are done by shipping to site a fully equipped container, consisting of six mill kits, power sources, wire and control equipment. We then set up to rebuild the mill rollers in situ. We start by using arc air gouging, if required, to remove material in problem areas, where delamination has occurred, for example. We will then usually decouple the mill gearbox and connect a Castolin Eutectic rotator linked to our control system outside,” Van Niekerk explains.
A maximum of six welding power sources and welding heads can be placed on positioners above the table or rollers and the welding is done using self-shielded flux-cored wires using an open-arc process. “This technology enables deposition rates of up to 60 kg per hour to be achieved, which enables the entire refurbishment to be completed within three to four days.
Wear plate manufacture
Hlakani is also now set up for the manufacture of Castolin Eutectic’s wear resistant chrome carbide-based CDP overlay plate. “We are in the process of setting up a flat-bed welding process to enable us to manufacture the Castolin Eutectic CDP range,” says Van Niekerk. ‘The facility will be able to produce CDP plate of up to 1.9×3.0 m, starting with a +4.0 mm chrome-carbide overlay on 6.0 mm substrate (6+4). We will also be offering a wider range of wear plates from Castolin such as laser-clad plate where thin, light wear plates are required and PTA tungsten clad plates. In the range we will also have special plates with wear thickness up to 30 mm of cladding for the mining industry.
“Hlakani site services also offer a full installation and site maintenance service for fabricated wear liners for mobile equipment, materials handling bins and chutes. Our new wear plate manufacturing capability enables us to supply custom wear plates that are locally produced and installed by our own people,” he says.