Advanced wear-resistant solutions for sinter plants
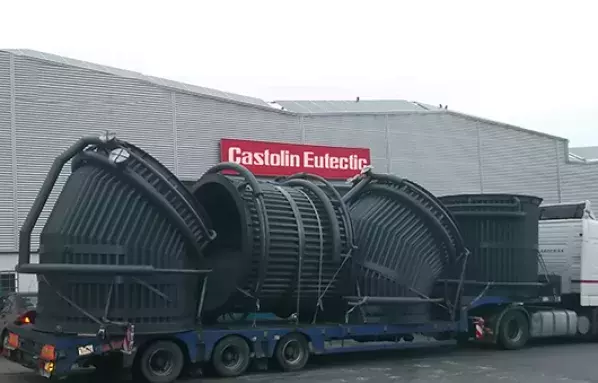
Abrasive materials, high temperatures and large mechanical loads experienced by components in iron and steel production create operational challenges. Martin Kirchgassner, Vice President and Chief Technology Officer of Castolin Eutectic, explains how hardfacing technology can extend the life of equipment to save operating costs and maximize operating life.
Sinter is essential for iron and steel production. However, it causes intensive wear on components in the sinter crusher, as well as other critical systems. For example, abrasive sinter dust in the atmosphere lands on the rails of overhead gantry cranes, causing wear and cracking on the steel tyres and creating risk of fatigue failure. The dust also causes excessive wear on the extraction fans and fume ducts that are used to maintain clean air and recover dust for recycling.
Intensive wear on sinter crushers and sieves
As the key equipment that breaks up sinter into correctly-sized particles, sinter crushers experience wear on multiple components but two of these bear the brunt of the effect. These are rotors and breaker bars. Sieves are another component that is subject to wear.
After being fed into the crusher by a chute, sinter is picked up by the teeth on a spinning rotor and smashed into a set of breaker bars. The rotor is made up of a series of discs mounted on a shaft. Each disc is fitted with two to four teeth that act as hammers to reduce the sinter. These teeth are exposed to heavy wear, meaning they often last less than a year.
Meanwhile, the breaker bars experience the heaviest wear of all, making them a priority area for adding wear resistance.
Another important component to consider is the sieve that grades sinter after the crusher. Castolin Eutectic offers a comprehensive range of wear-resistant sieves with round, square or oval apertures manufactured from 3mm thick or higher, perforated sheets. The company also manufactures tailor-made solutions according to specific customer requests: hot sieves, cold sieves, hot chutes of all shapes, forms and materials.
Traditional methods to extend crusher life
Sinter is hot when it arrives at the crusher, therefore operators need to take care when considering how to increase durability. This is particularly important as the surface hardness of materials (and therefore their wear resistance) reduces as temperature rises.
The simplest action is for operators to accept they will need to carry out regular overhauls and maintenance to rectify heavy wear. That may be acceptable for some sites. However, wear rates vary, depending on temperature, loading and design. Therefore, some operators need to fit wear resistant liners or inserts, apply wear resistant hardfacing coatings, use wearplates and integrate water cooling.
An alternative is to add a hardfacing coating in key areas. A challenge for rotors is that hardfacing may not provide enough protection and the base material may wear away before the coating.
Furthermore, the thick hardfacing layer needed on breaker bars typically has lower heat transfer coefficient than structural steel. This leads to build-up of heat and ultimately decreases the wear resistance. In addition, cracks can develop and propagate in the thick coating, causing spalling.
It is also possible to integrate water cooling systems into breaker bars to protect surface hardness and therefore durability. However, this carries additional operational requirements and risks, for example of water leakage and build-up of calcium scale.
High-performance hardfacing boosts durability for sinter crushers
When it comes to sinter crushers, additional protection is often needed for rotor discs and their teeth, as well as breaker bars and sieves. This can be achieved with advanced hardfacing technology, which extends the service life of components by a factor of three to reduce maintenance outages and preserve crusher productivity.
This approach is based on highly wear-resistant alloys capable of withstanding temperatures of 400 °C and higher. To maximize durability, we use a system approach, with the alloy being anchored to the structural steel of the components using a specially developed welding pattern.
Using just a thin wear resistant layer of hardfacing improves durability as heat can transfer away from the surface, protecting the surface hardness. In addition, it minimizes the potential for spalling as it is applied as a single layer directly onto the softer structural steel.
A further benefit of protecting the surface is that the crusher parts will retain their original geometry for longer. This is important to avoid equipment becoming worn and rounded, which would reduce the efficiency of the sinter crusher. Therefore, maintaining the shape of parts protects efficient operation for longer.
Protection against airborne particles
Different types of welding wire can be used to repair the outer layer of blades of ventilation fans that extract dust from sinter plants.
Elsewhere in the air handling process, life of fume ducts can be extended with a thermal spraying process to apply a fine metallic coating of up to 0.8 mm. This provides high wear resistance against the erosion and corrosion of abrasive airborne dust. It is important for this type of coating to bond well with the substrate with limited distortion.
Pioneering industrial sustainability
The abrasive materials in iron and steel mills represent significant maintenance requirements due to excessive wear on equipment such as sinter crushers, sieves, gantry crane wheels and the fume ducts in air-handling systems.
However, advanced wear-resistant coatings can significantly extend the life of key components, ensuring that critical equipment works efficiently, helping plants to consume less energy and reduce CO2 footprint.