Oil and Gas
Choose a category
-
ImageTool joints
-
ImageWear sleeves and cutter wheels
-
ImageHole Openers and drill bits
-
ImageMills and stinger pistons
-
ImageBall valves and sprayed mandrels
-
ImageStabilizers and shafts
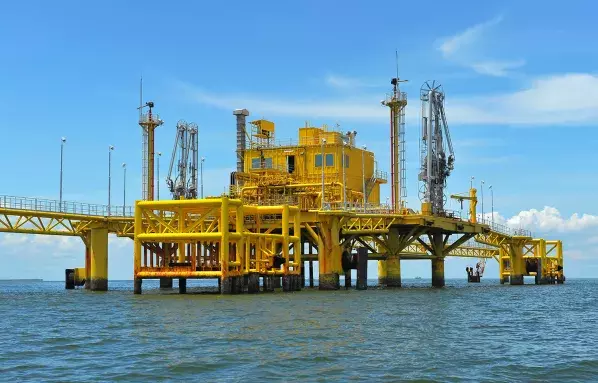
Today’s drilling challenges
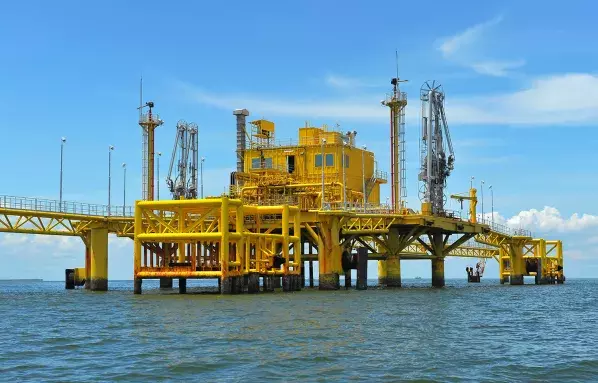
As average well depths have increased over the past decade, directional and extended-reach drilling have become more commonplace. These wellbore trajectories, with their highly deviated paths (ERD) and associated increases in torque and drag, have exerted unprecedented force on the drill pipe, surpassing all previous stress level limits. These trajectories in turn, create severe wear conditions on both the casing and drilling string, which is becoming increasingly detrimental for drilling operations.
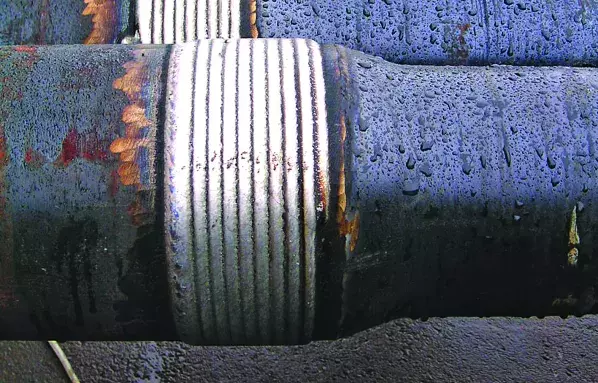
Avoid catastrophic tool joint failure
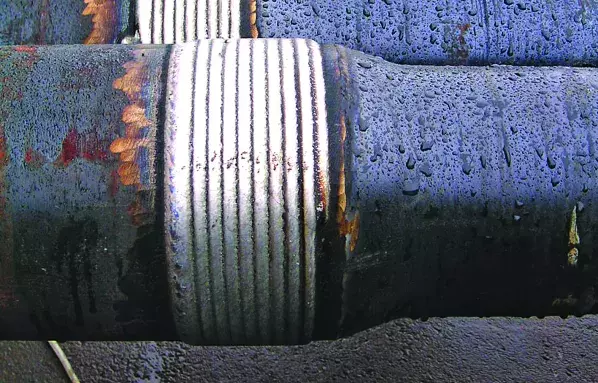
Hardbanding has long been acknowledged as an effective means of preventing tool joint wear. During the 1990’s, tungsten carbide-based hardbanding was in widespread use and was determined to be the primary cause of casing wear. However the absence of hardbanding, while slowing casing wear to a small degree, allowed the tool joints to wear at an accelerated rate, lessening the torsional capacity of the drill pipe and putting drilling operations at a serious risk. The challenge was to discover a balanced, simultaneously effective solution between both casing wear defense and tool joint protection, which is caused by the worsening conditions associated with highly deviated ERD wells. Previous casing friendly alloys reduced casing wear, but produced unacceptable tool joint wear as a consequence. Crack-prone design flaws were also present, as widespread cracking of the alloy material often ensued. This caused catastrophic tool joint failure and in some cases, even the failure of the hardbanding itself, due to tool joint spalling.
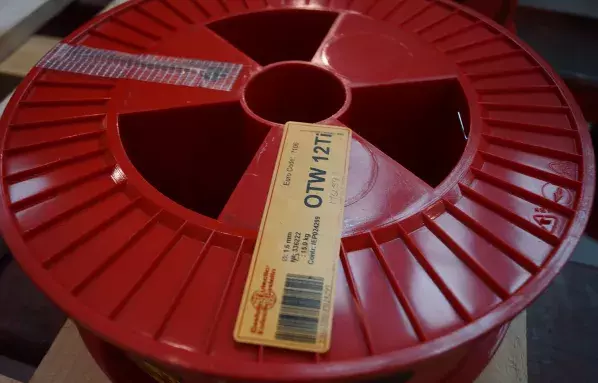
All formulated and manufactured in our own modern plant in Ireland
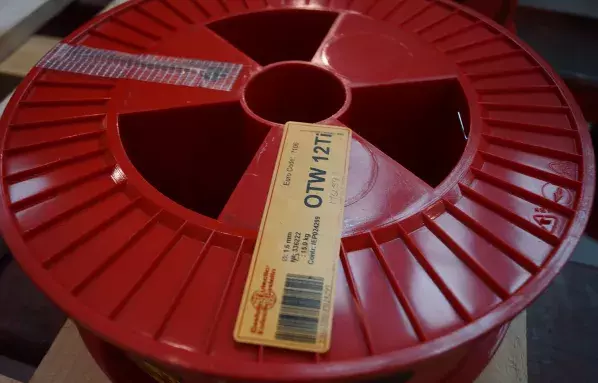
Castolin Eutectic has been performing hardbanding in the Norwegian market for more than 15 years. Due to excellent co-operation between Castolin Eutectic and Statoil, there has been very successful development, use and approval of our innovative OTW alloys. Today Statoil approves OTW 12Ti, OTW 16XS and the non-welded, patented MX5 coating for drilling. During development of the OTW range, Castolin Eutectic constructed its very own, unique hardbanding C-Wear testing machine. The machine tests encompass:
• Casing material combined with full-size, hardbanding alloy-infused wear samples
• Specific mud parameters, measuring tool-joint, open hole and casing wear rates.
• Established hardbanding coating friction dynamics.
In addition to this, we use an automated Micro Hardness Machine, a G65 Abrasion Wear-Test Machine and ICP / XRF Chemical Analysis Units, employing a well trained, customer-oriented technical team. Our global crew of highly qualified engineers tests OTW products on active field components, under the most extreme drilling conditions. These harsh environments provide the necessary criteria for understanding severe wear phenomena and set the standard by which we measure our product integrity.
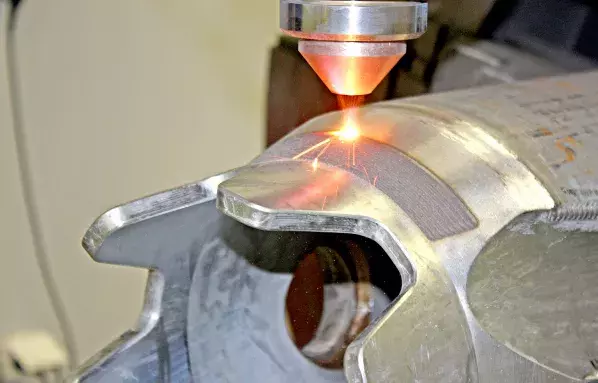
Specialist in non-mag steel coating solutions
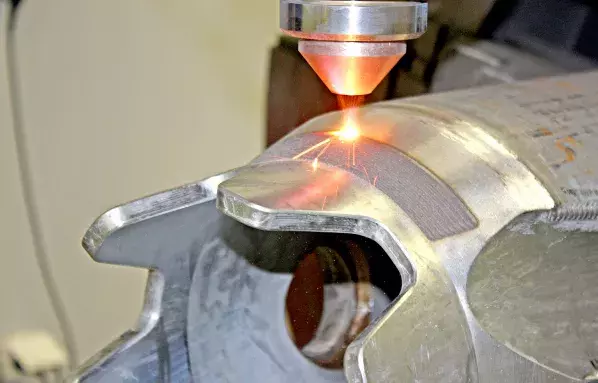
- New production of wear sleeves and stabilizers for steerable drilling systems, logging systems, MWD tools, LWD tools, drilling motor sleeves
- Industry leader and specialist in non-mag steel coating solutions including laser cladding
- Coatings include tungsten carbide rods and tungsten carbide tiles
- Approved and certified Quick-Tip applicators
- Short delivery of non-mag wear sleeves; non-mag materials at stock at all times to allow for short delivery times and on-demand special solutions
- Sizes up to 17 ½ inch: special solutions on request.
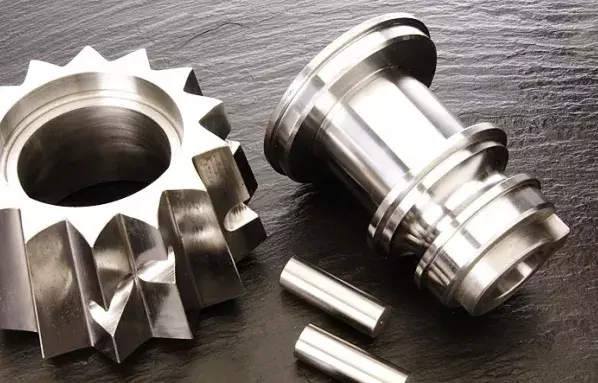
2 to 7 times longer service life than the original material
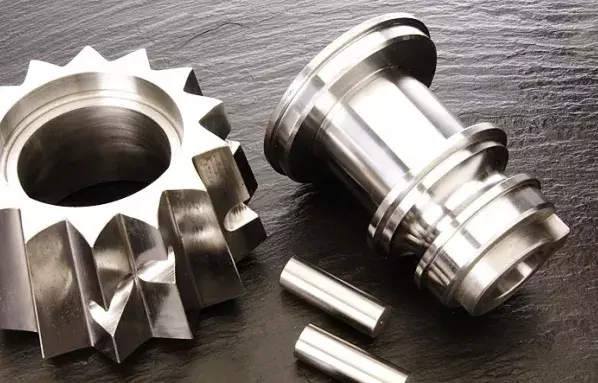
The cutter wheel designs we provide include both straight and twisted teeth. The number of teeth, angles and shapes vary. The Trio OilTec Services unique solution of special base materials, heat treatment, combined with wear resistant coatings significantly extends cutter wheels service life. Experience shows that our cutter wheels last 2 to 7 times longer than the original material and existing coatings on the market to day.
With these designs and material choice, the wear on the "Hole Opener" saddles is simultaneously reduced. This is due to the fact that cutter wheels have better wear resistance and the contact to saddles becomes less aggresive. In addition, the speed of hole opening increases.
Advantages:
- Longer life of cutter wheel
- Less wear on "Hole Opener" body/saddles
- Reduced maintenance cost
- Faster hole opening

We deal with large-scale parts up to 10 tons

- Inspection, service and maintenance of hole openers and large drill bits
- Body repair, heat treatment and wear protection with wolfram carbides
- Rebuilding and adaptations
- Own production of high quality cutter wheels
- Handling of bodies up to 10 tons and 6m length
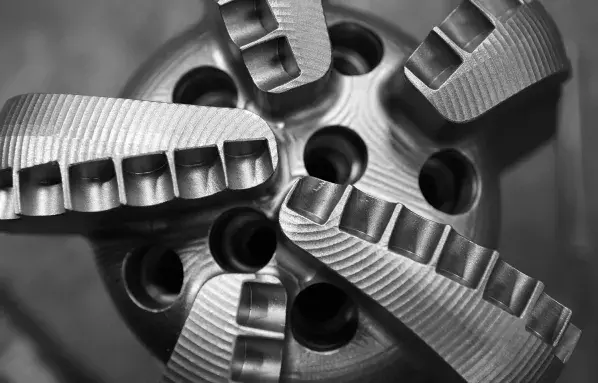
Service, maintenance and wear protection
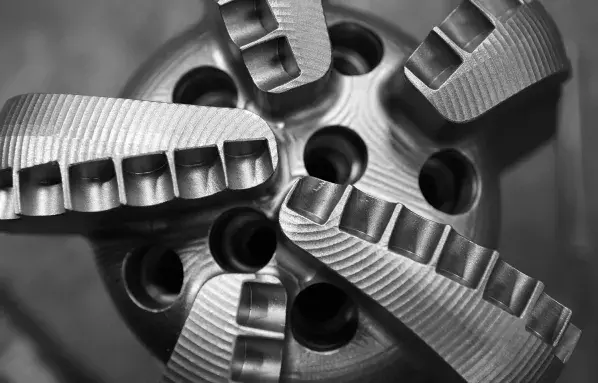
- Inspection, service and maintenance of matrix and steel-bodied drill bits
- Silver brazing of diamond inserts
- Redressing of cutter wheels
- Shoulder wear protection

We are approved applicators for precision dressing

- Redress of all different downhole mills
- Procedures for applying tungsten carbide brazing
- Silver brazing with diamond cutters
- Approved applicator for precision dressing with cutting inserts, wolfram carbide and diamonds

HVOF thermally sprayed with wolfram carbide coatings

- Precision grinding with diamond wheel CNC controlled grinding machines
- HVOF thermal spray with wolfram carbide coatings
- Super polishing
- Procedures established for applying high quality coatings on all stinger pistons used as part of plug systems
- Diameter up to 630 mm, 3000 mm length and total weight up to 3 tons
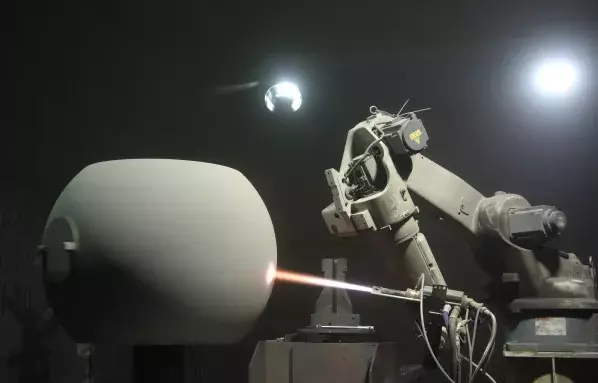
Protected by HVOF coatings
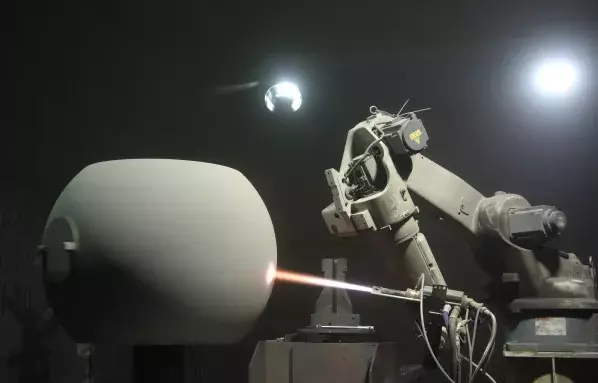
- HVOF Thermal Spray with wolfram carbide coatings
- Electroplating for selective spot repair and coatings for wear and corrosion protection
- Ball valve grinding to the finest tolerances
- Super polishing and lapping
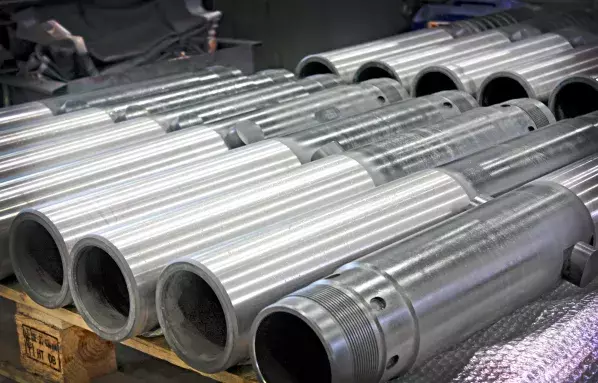
Unmatched wear resistance for mandrels up to 3 tons
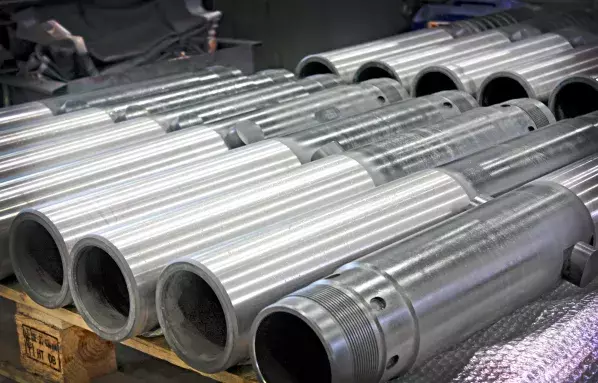
- Precision grinding with diamond wheel CNC controlled grinding machines
- HVOF thermal spray with wolfram carbide coatings
- Super polishing
- Procedures established for applying high quality coatings on all mandrels used in the oil & gas industry, including jars, gas-lift mandrels and packer mandrels
- Diameter up to 630 mm, 3000 mm length and total weight up to 3 tons
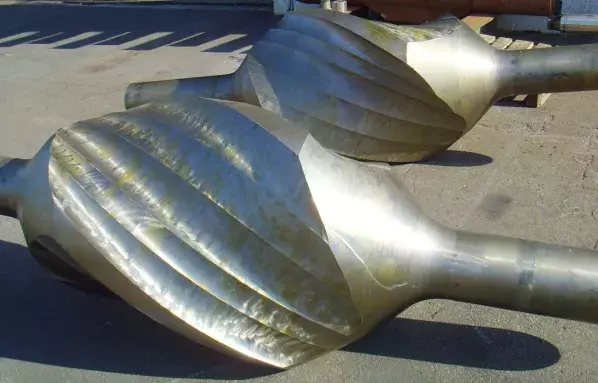
Rebuilding, crack welding, heat treatment and wearfacing
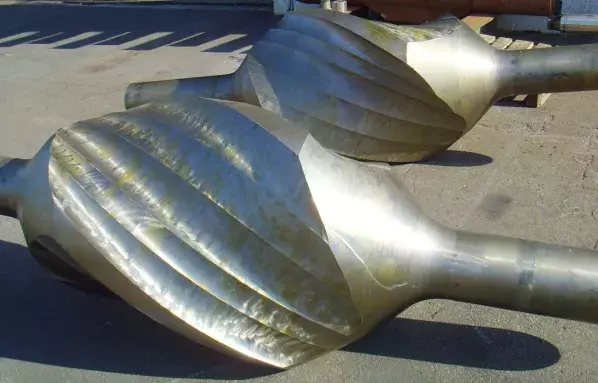
- Inspection, service and maintenance of all stabilizers used in the drilling industry
- Non-mag stabilizer specialist
- Body repair and crack welding, heat treatment and wear protection with wolfram carbides
- Coatings include tungsten carbide rods and tungsten carbide tiles
- Applicator of non-mag special coatings, including laser coating
- Approved and certified Quick-Tip applicator
- Rebuilding and adaptations
- Big offshore grinders for handling of bodies up to 10 tons and 6m length, OD up to 48 inches
- Repair of all drilling stabilizers in non-mag and steel
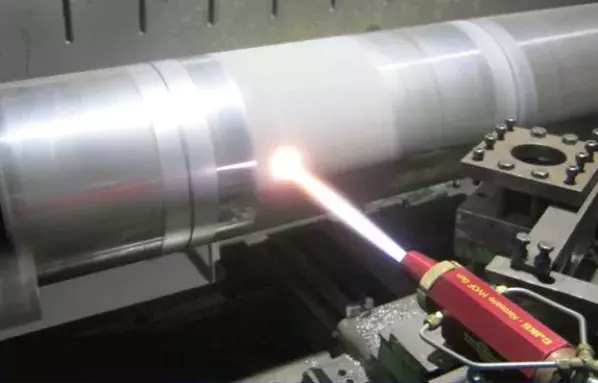
Massive components with flawless surface finishing
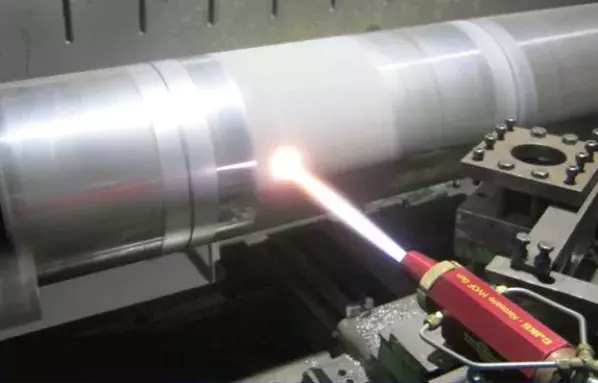
- Precision grinding with diamond wheel CNC controlled grinding machines
- HVOF thermal spray with wolfram carbide coatings
- Surface polishing
- Diameter up to 630 mm, 3000 mm length and total weight up to 3 tons
Discover other industries
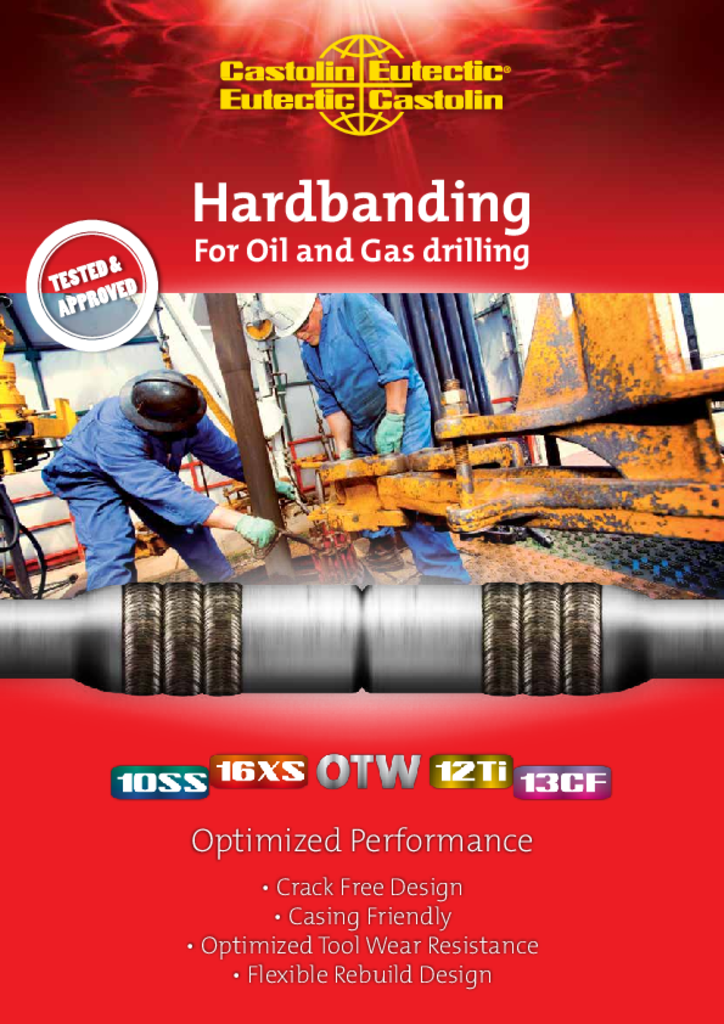
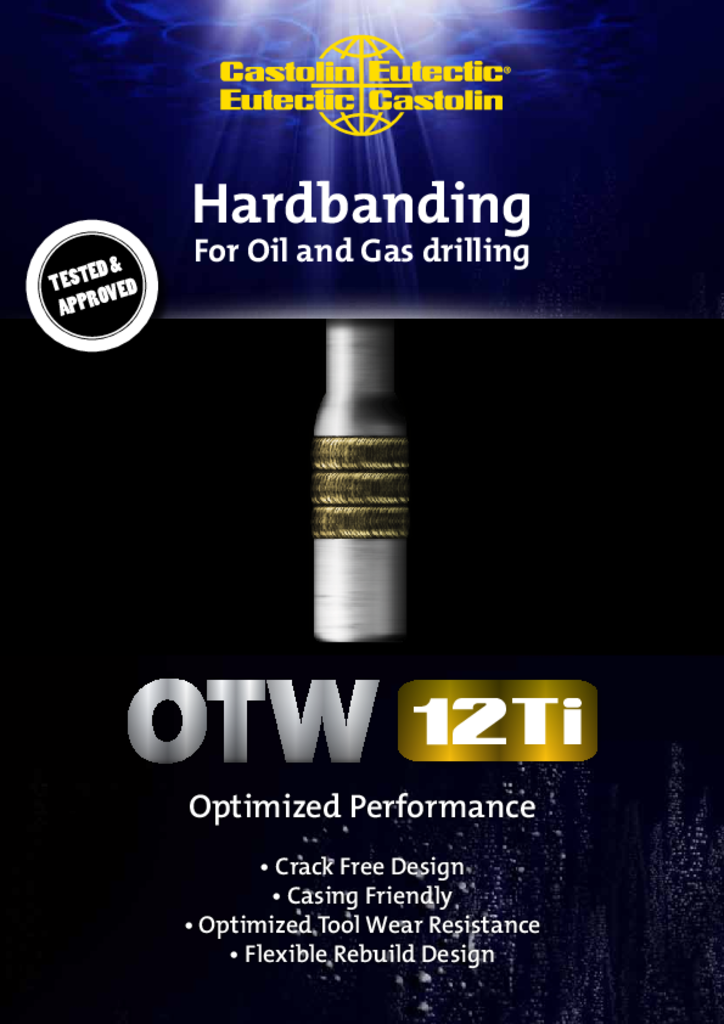
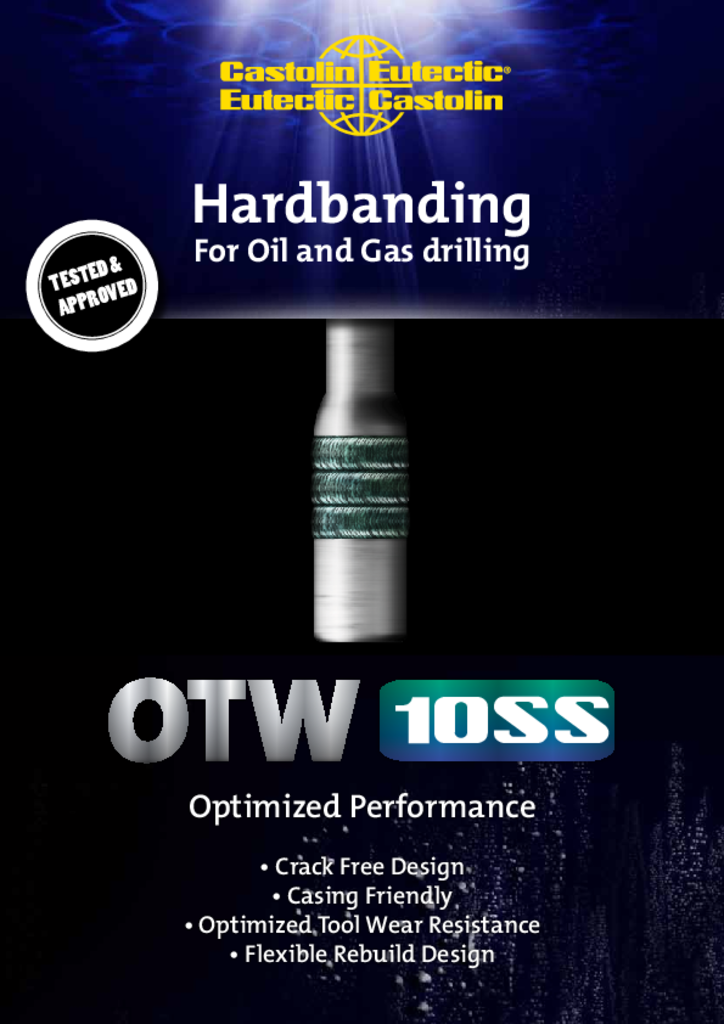