Steel
Choose a category
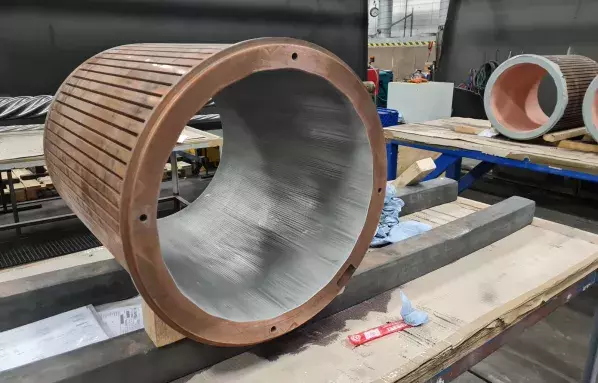
Coatings for the full range of steel manufacturing and coating processes
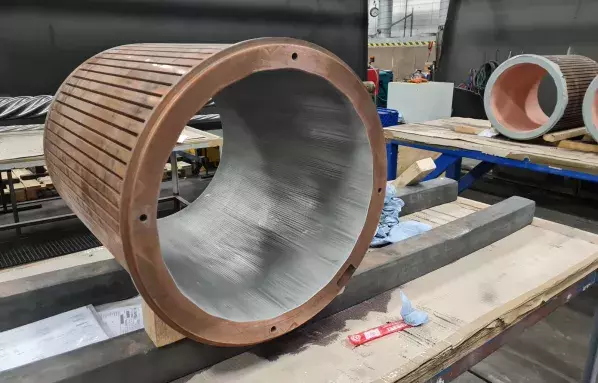
Components – The Castolin Eutectic workshop in Newcastle has capability to apply coatings for the full range of steel manufacturing and coating processes:
- Raw Material Processing – Feed Hoppers, Staves, Blow Pipes, Tuyere, Plate Coolers, Industrial Fan Impellers, Industrial Fan Casings, Ducting, Feed Screws, Wind Boxes, Grinding Rolls
- Steel Making – BOF Injection Lances
- Casting – Slab Moulds, Bloom Moulds, End Plates, Comb Plates, Grid Plates, Foot Rolls,
- Rolling – Bridle Rolls, Deflector Rolls, Dancer Rolls, Steering Rolls, Tensiometer Rolls, Cleaning Rolls, Table Rolls
- Heat Treatment – Skid Post , Furnace Rolls, Catenary Rolls, High Temperature Seal Rolls
- Coating – Galvanising Pot Rolls, Sleeves & Bushes, Aluminising Pot Rolls, Sleeves & Bushes, Conducting Rolls
Applicable Coating Technologies – The Castolin Eutectic workshop in Newcastle applies a range of coating technologies for the extension of component lifetime:
- Corrosion Resistant Coatings – MoniPlex®, NiAl, MCrAlY
- Thermal Barrier Coatings – AlTi, NiAl, MCrAlY, ZrO2 XY2O3, Al2O3, 3Al2O32SiO2 (Mullite)
- Wear Resistant Coatings – Cr2C3-NiCr, WC-Co, WC-CoCr, Al2O3, Al2O3-TiO2, Cr2O3
- The Castolin Eutectic workshop in Newcastle manufactures and apply specialist SealPlex™ and MoniPlex™ slurries, and other commercially available sealants as a method of coating densification to remove porosity and improve the corrosion resistance of the as sprayed coating and have the ability to strip old coatings to offer the potential for repair and overhaul of components.
- Other materials available upon request
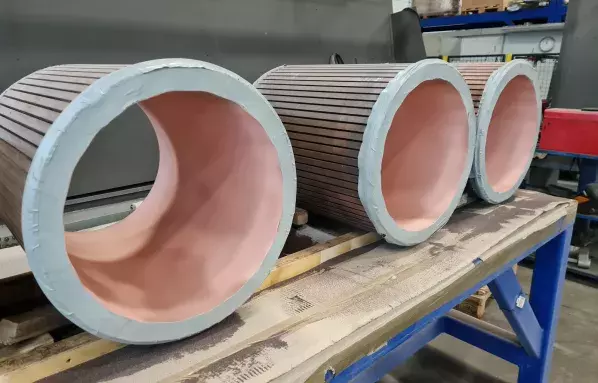
Coatings to extend the lifetime of critical components
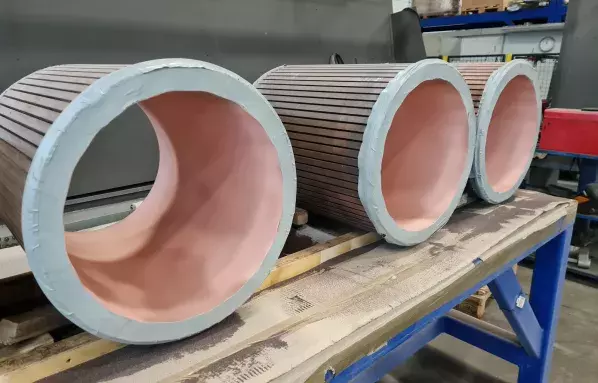
Components – Castolin Eutectic wokshop in Newcastle specializes in the application of coatings to extend the lifetime of critical components within vertical and curved casting operations:
- Bloom Moulds
- Billet Moulds
- Slab Moulds
- Broadface Plates, End Plates, Comb Plates, Grid Plates, Broadface Plates, Narrow Plates, Foot Rolls, Casting Rolls
Key Benefits – Castolin Eutectic wokshop in Newcastle ConCast coating technology has a series of key benefits when applied to casting operations:
- Highly dense coating where coating porosity ~0.2%
- Low coating oxide formation ~0.6%
- Increase coating hardness versus plated coatings > 1200HV
- Reduced friction and abrasive wear with increased in lifetime versus conventional coating solutions
- Chemical Inertness and reduced propensity for slab cracking, slab shape, slab sticking, mould powder consumption and mould usage
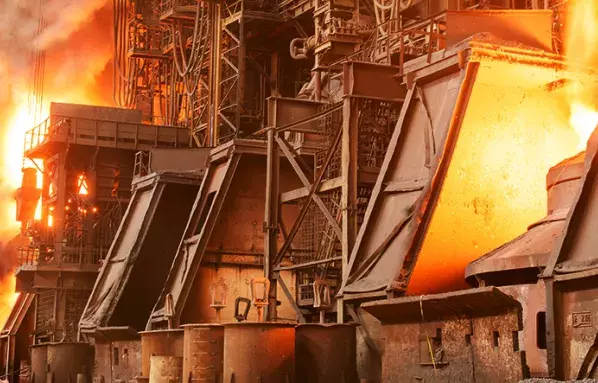
Blast Furnace components
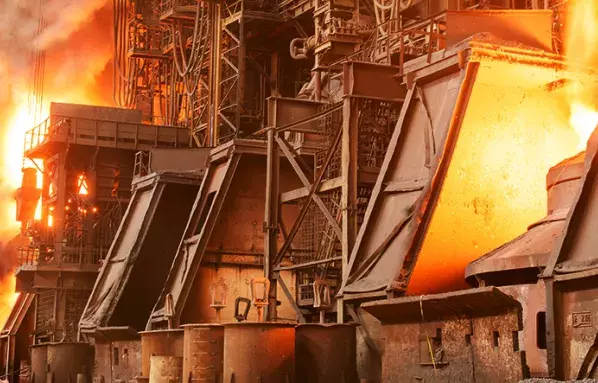
Extensive in-process damage to the external diameter of the Tuyere Cooler component, used in Blast Furnace operations, is a common occurrence and can lead to reduced processing capability and equipment downtime. This is especially pertinent when the substrate damage results in the Tuyere becoming lodged in the parent housing and having to be forcibly removed. Tata Steel together with Castolin Eutectic have developed a thermal spray deposition which would help negate the potential damage to the component and thus extend its useful processing life by reducing the build up and adhesion of Blast furnace by-products.
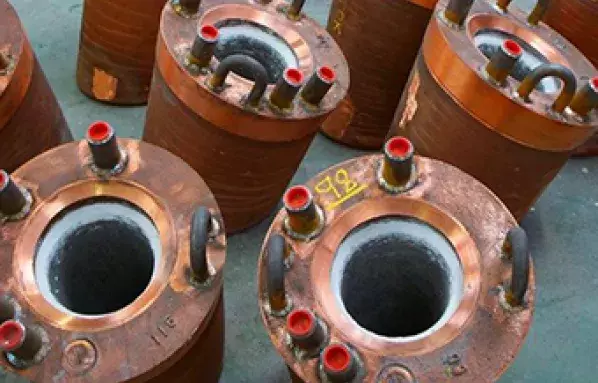
Tuyere coolers that exceed your expectations
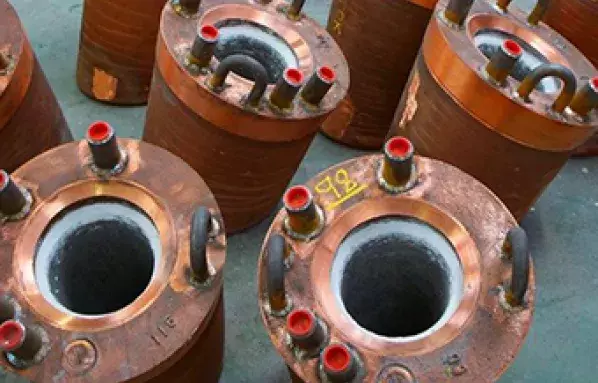
After extensive trials a composite coating structure comprising of a High Velocity Oxy Fuel (HVOF) deposited Nickel-Chromium coating together with a thermally converted slurry addition was used to protect the affected external surface. This coating produces a pore-free surface which inhibits the adhesion of the process by-products whilst protecting the substrate from extensive wear by chemical erosion.
Castolin Eutectic R&D Manager United Kingdom
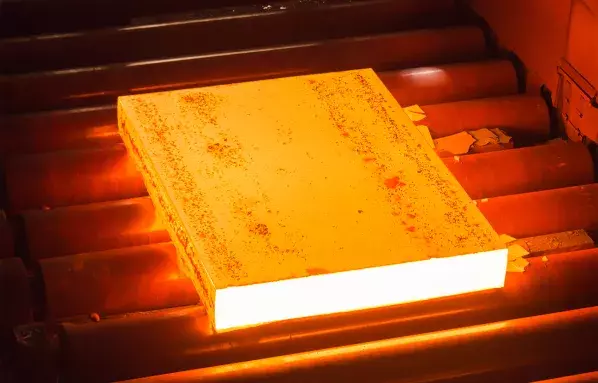
CastCoat from Castolin Eutectic
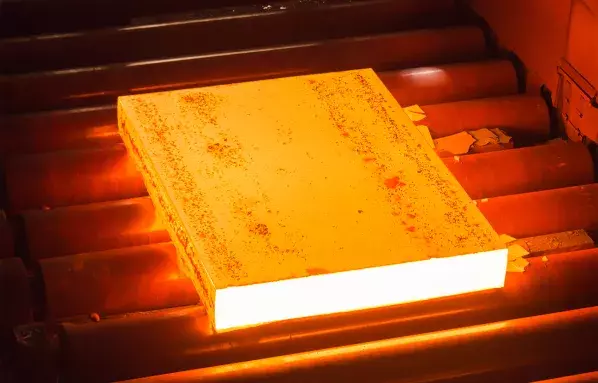
The CastCoat hard composite coating was developed by the advanced Castolin Eutectic workshop in Newcastle, UK, for steel industry applications in particular for coating continuous Caster copper mould plates, for more than 20 years. Tests have shown that the coating is tougher than any other copper mould plate coating available. It has a low coefficient of friction which helps reduce sticker alarms and the coating is inert to liquid steel and casting powders. The coating system has no effect on mould level detectors or electromagnetic stirrers. It has also been proven that the coating has negligible effect on heat transfer rates.
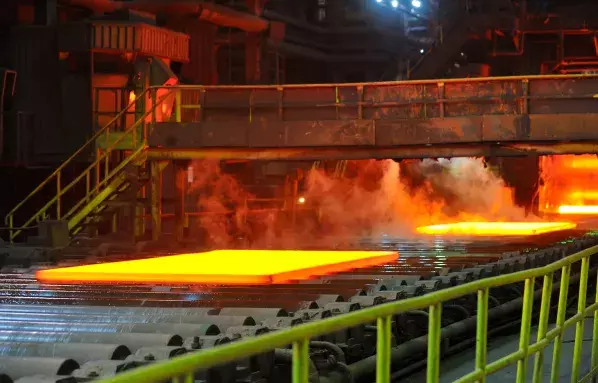
Now a mature technology
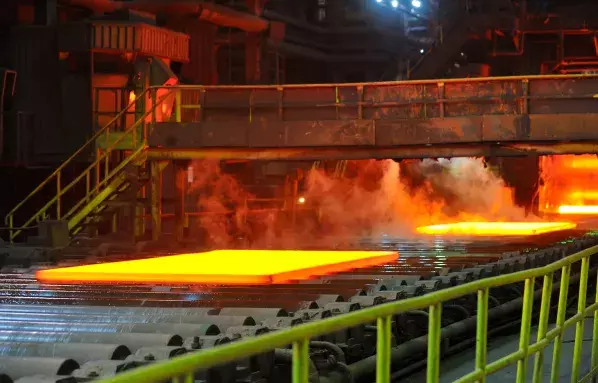
With years of field data behind the coating, significant copper plate life improvements have been demonstrated: 3 – 4 times for thick slab casters and up to 6 times for thin slab caster narrow plates, accompanied by improved product shape. In operation, the coating has been shown to enable extended casting runs through dramatic increases in wear resistance. Eventual progressive degradation of the coating occurs due to the thermal fatigue in high stress positions. Now a mature technology with a worldwide customer base, CastCoat continues to provide users with reduced costs/tonne.
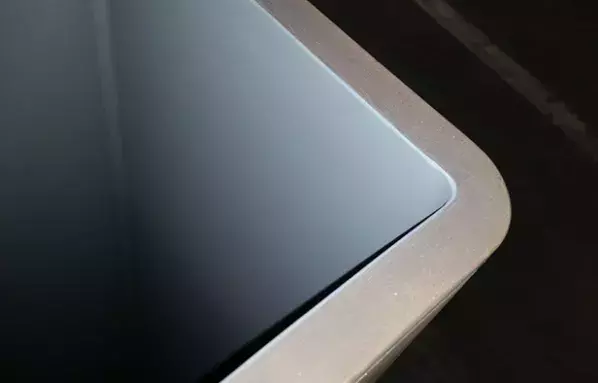
New compact HVOF device
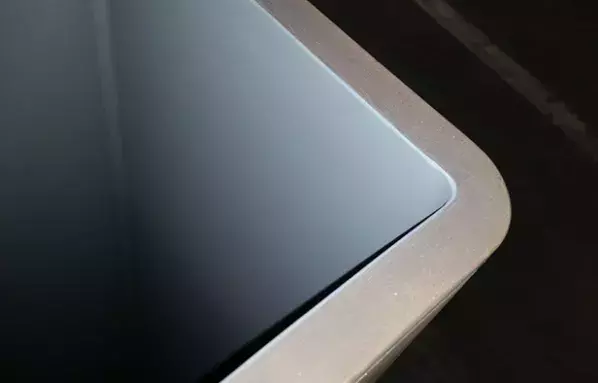
By coating all four faces of the mould, dimensional stability is retained throughout the campaign, leading to sustained and effective product shape and shell growth. The lack of appreciable wear means longer campaigns are possible between mould exchanges, achieving higher caster availability. In addition, the protection offered by the coating gives extended copper plate life, resulting in annual copper savings and delivering significant reductions in both on and off-line maintenance costs. With the recent development of a compact HVOF device, the CastCoat Composite Coating can now be applied to tube moulds.