Choose a category
-
On-site projects
-
Workshop capabilities
-
Visit Us
-
International Customer Approvals
-
Coating Evaluation & Laboratory
-
Floor Equipment
Our mission is to develop applications and solve customer problems. Since the mid 1930´s, Castolin Eutectic has offered industry a range of specialised training courses, which covers all aspects of the welding processes, e.g. MMA, MIG, TIG, brazing, soldering and thermal spraying.

For welders, engineers or managing directors

Our commitment to excellent customer service means providing first-class training available globally to customers and end-users. Castolin Eutectic has trained thousands of technicians from all over the world and training centres have been established in most countries with training programmes offered in a wide variety of languages. We offer a wide range of courses starting from one-day welding courses to full-week maintenance seminars. From welders to engineers, researchers and managing directors - there´s no limit to the range of technical and professional people trained by Castolin Eutectic in all aspects of industrial cost-savings, wear, repair and preventive maintenance.
Advanced surface engineering
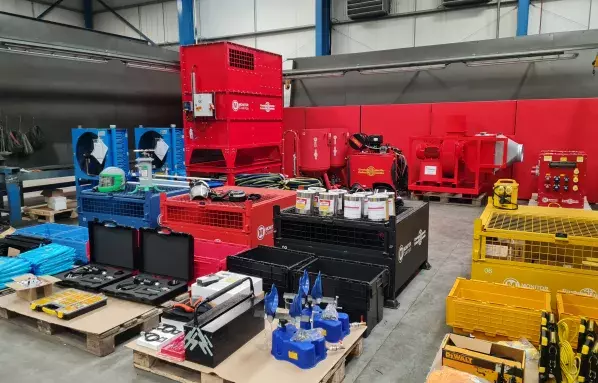
Tailored Coating Services Across Diverse Industries
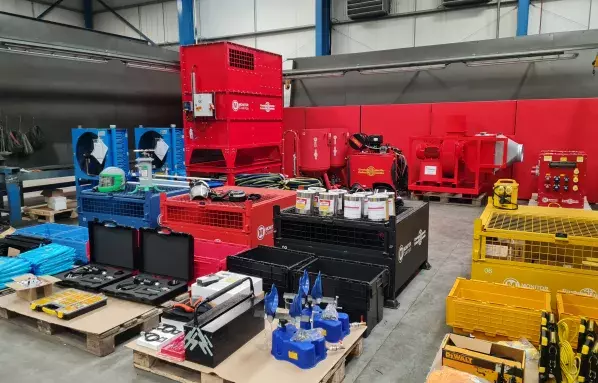
Process Descriptor – Castolin Eutectic workshop in Newcastle offers offsite bespoke work packages through a range of different thermal spray coatings on site at customer facilities across a wide range of industry sectors. We are able to develop and support risk assessment for projects and mobilise personnel and equipment to site for the duration of project activities. We can carry out cleaning, blasting, welding, spraying and sealant cure activities to extend lifetime of critical plant at the customer facility.
Applicable Industries – Marine & Defense, Petrochemical, Waste to Energy
Materials (Broad Classification) – AlMg Alloys, AlTi Alloys, CuAl Alloys, CuP Alloys, CuZn Alloys, FeCr Alloys, FeNiCr Alloys, Molybdenum, NiAl, NiCr Alloys, NiMoCr Alloys, SnCu Alloys, TSA Alloys, Zn, ZnAl, other materials available upon request
Process Capacity – Castolin Eutectic workshop in Newcastle can provide fully containerised blasting and coating systems for site work:
Customer Site Services: Coating Removal, Blast, Spray & Sealant Cure across unlimited work areas
Special Considerations – Castolin Eutectic workshop in Newcastle manufactures and applies specialist SealPlex™ and MoniPlex™ slurries, and other commercially available sealants as a method of coating densification to remove porosity and improve the corrosion resistance of as sprayed HVOF coating.
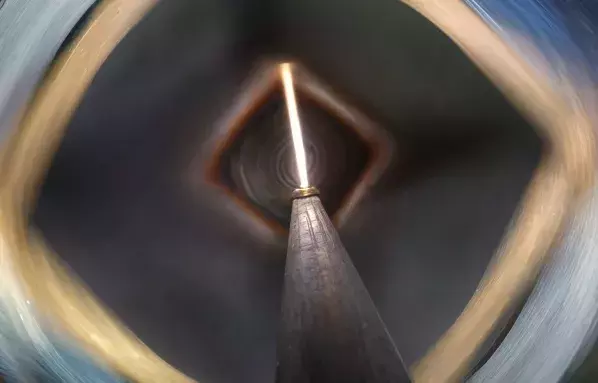
Capabilities
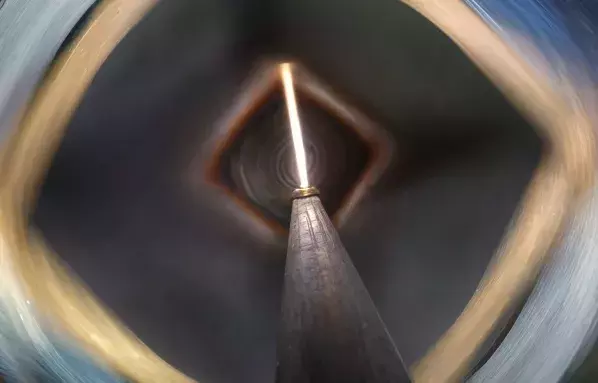
- Compact High High Velocity Oxy Fuel (cHVOF) (Internal)
- High Velocity Oxy Fuel (HVOF) (External)
- Air Plasma Spray (APS)
- Low Pressure Plasma Spray (LPPS)
- Thermally cured chemical Slurry Coatings (MoniPlex/SealPlex)
- Heat Treatment
- CNC turning, milling and grinding service
- Arc Spray – including on-site operations
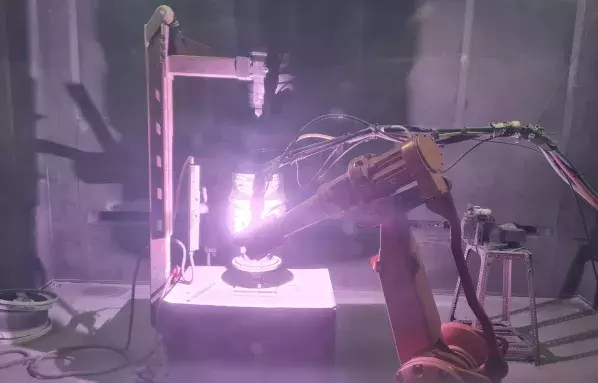
Air Plasma Spray coating
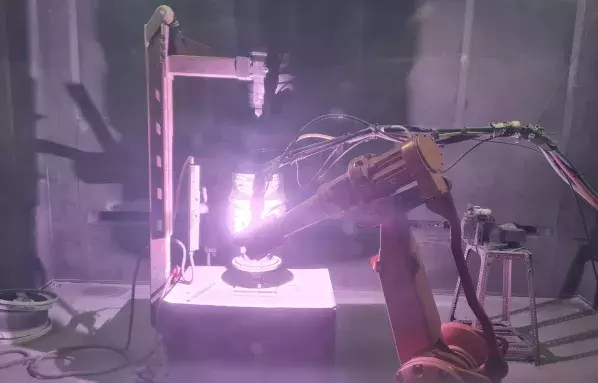
Process Descriptor - Air Plasma Spray coating is a plasma process where particles are melted and accelerated towards the substrate at extremely high temperature to produce a dense and uniform coating. The high temperature associated with the plasma allows for the melting of high temperature materials. The versatility of the plasma process allows for specialty materials to be applied as coatings including polymers where coating materials can imbue specialist properties including chemical resistance, lubrication and electrical insulation as well as resistance to abrasion, corrosion and thermal induced failures.
Materials - Abradables – AlSi-PE, AlSi-hBN, AlSi-Graphite, Ni-Graphite, NiCrFe-hBN, MCrAlY-hBN-PE, MCrAl-Bentonite, YSZ-PE, DySZ-PE, Al2O3, Al2O3/TiO2, Cr2O3, Cr2O3/TiO2, MCrAlY, NiCr, NiAl, WC/Co, TBC – ZrO2 XY2O3, Pure Molybdenum & Molybdenum alloys, Pure Si, Pure Ta, Pure Ti, TiC, TiO2, Y2O3, Self-Fluxing Ni alloys, Self-Fluxing Co alloys, other materials available upon request
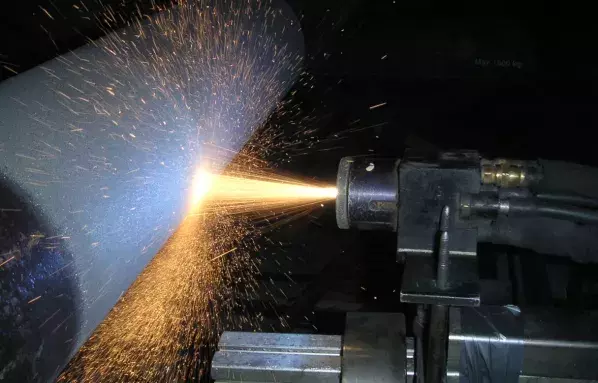
Electric arc spray method where the wire is atomized with compressed air
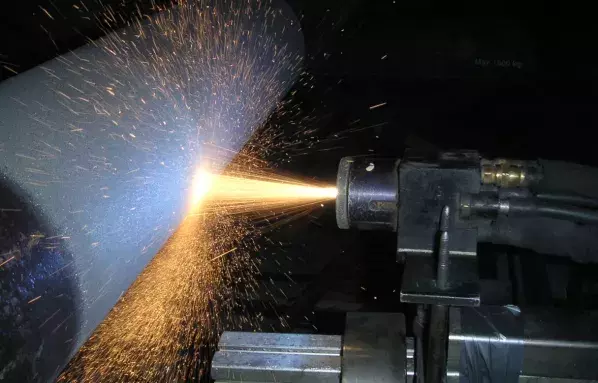
Process Descriptor – Arc Spray is an electric arc spray method where the wire is atomized with compressed air to create the spray stream to achieve high deposition rates and flexibility for workshop and site coating application. Arc Spray is used to apply a wide range of solid or composite metallic feedstocks. Flexibility of the process allows for large work areas to be coated including carrier deck in the marine environment and waste to energy boiler systems.
Materials (Broad Classification) – AlMg Alloys, AlTi Alloys, CuAl Alloys, CuP Alloys, CuZn Alloys, FeCr Alloys, FeNiCr Alloys, Molybdenum, NiAl, NiCr Alloys, NiMoCr Alloys, SnCu Alloys, Zn, ZnAl, other materials available upon request
Process Capacity
- Castolin Eutectic has two Air Plasma bays which can accommodate a wide variety of component sizes and geometries:
- Bay 2: 7000mm length x 800mm OD x 3000Kg
- Castolin Eutectic Site Capability: Unlimited
- Customer Site Services: Coating Removal, Blast, Spray & Sealant Cure across unlimited work areas (Carrier Deck and Waste to Energy boilers)
Special Considerations – The Castolin Eutectic workshop in Newcastle manufactures and applies specialised SealPlex™ and MoniPlex™ slurries, and other commercially available sealants as a method of coating densification to remove porosity and improve the corrosion resistance of as sprayed Arc Spray coating.
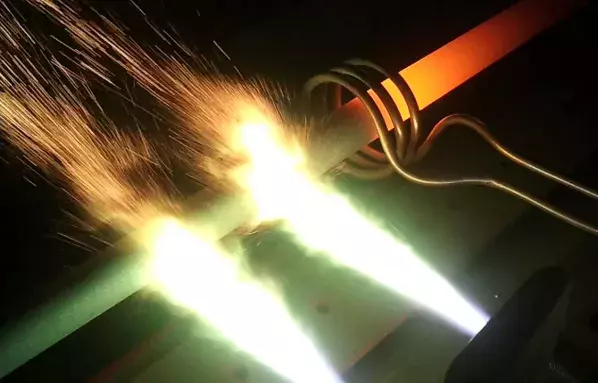
Low velocity thermal spray coating
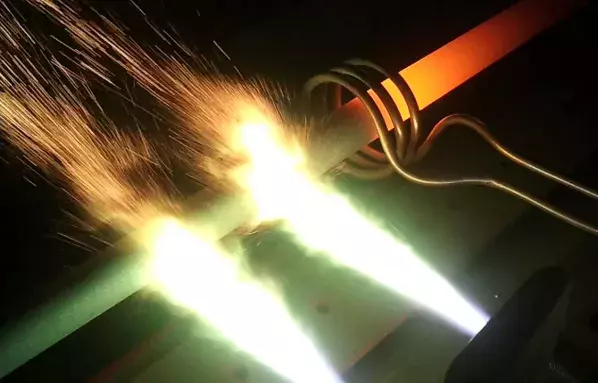
Process Descriptor – Flame spray is a low velocity thermal spray coating process where oxygen is used along with a fuel source (typically acetylene) to create a flame which applies metallic, ceramic or cermet materials with high deposition rates. The flame spray process is compatible with carbon and stainless steels, and nickel alloy base materials. Depending on flame spraying technique, the coatings produced can be fully dense or require post application fusion of the coating deposit, when the coating materials used are self-fluxing in nature.
Materials (Broad Classification) – Eutalloy, RotoTec, ProXon, MetaCeram, CastoPlast, CeraTuff. Other materials available upon request
Process Capacity
- Castolin Eutectic has a range of thermal spray bays which can be fitted to perform flame spraying and can accommodate a wide variety of component sizes and geometries:
- Bay 1: ___mm length x ___mm OD x ___Kg (weight limit)
- Bay 1a: ___mm length x ___mm OD x ___Kg (weight limit)
- Bay 2: 7000mm length x 800mm OD x 3000Kg
- Bay 2a: ___mm length x ___mm OD x ___Kg (weight limit)
Special Considerations – Due to preheat requirements for flame spraying methods, this process isn’t compatible with all base materials and the nature of the coating application method needs to be considered. The heat input associated with flame spray method and fusion operations will result in a change in mechanical properties of the base material.
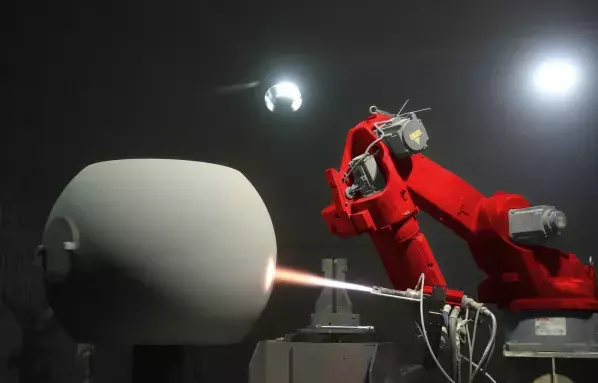
High Velocity Oxygen Fuel (HVOF) coating
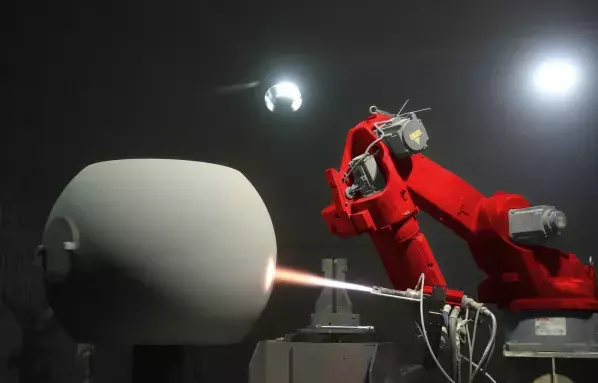
Process Descriptor – High Velocity Oxygen Fuel (HVOF) coating is a high velocity thermal spray process utilising oxygen and kerosene as a fuel source to apply metallic, ceramic or cermet thermal spray materials onto a wide range of complex components across most industry sectors. The high velocity process creates repeatable highly dense coatings with excellent coating adherence. HVOF application of coating materials protect against a range of common industrial failure modes including abrasion, corrosion, fatigue, oxidation and high temperature to extend component lifetime.
Materials (Broad Classification) – FeCrNiMo, FeCr, NiCr, NiAl, Self-Fluxing Ni alloys, MCrAlY, CoCrWBSi, CoCrNiW, CoCrWSiC, CoMoCrSi, Self-Fluxing Co alloys, Cu Alloys, Pure Molybdenum & Molybdenum alloys, Cr2C3/NiCr, WC/Co, other materials available upon request
Process Capacity
- Castolin Eutectic has four HVOF bays which can accommodate a wide variety of component sizes and geometries:
- Bay 1: XXXmm length x XXXmm OD x XXXKg (weight limit)
- Bay 1a: XXXmm length x XXXmm OD x XXXKg (weight limit)
- Bay 2: 7000mm length x 800mm OD x 3000Kg
- Bay 2a: XXXmm length x XXXmm OD x XXXKg (weight limit)
Special Considerations – The Castolin Eutectic workshop in Newcastle manufactures and apply specialist SealPlex™ and MoniPlex™ slurries, and other commercially available sealants as a method of coating densification to remove porosity and improve the corrosion resistance of as sprayed HVOF coating. HVOF is a replacement technology for hard chrome plating offering improved wear and corrosion resistance, coating uniformity and adhesion. The Castolin Eutectic workshop in Newcastle has the ability to strip old coatings to offer the potential for repair and overhaul of components.
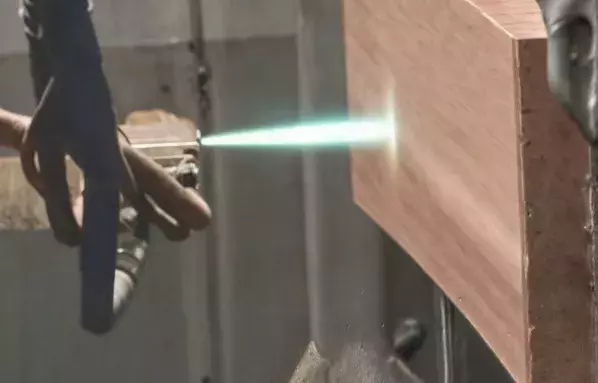
The Compact High Velocity Oxygen Fuel (cHVOF) coating
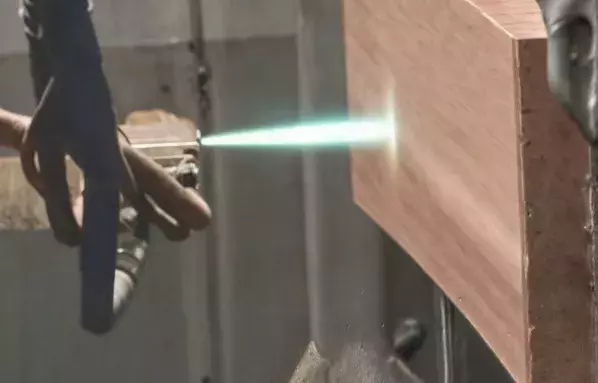
Process Descriptor – The Compact High Velocity Oxygen Fuel (cHVOF) process is a patented Castolin Eutectic technology that optimises combustion, powder injection and fuel mixing within a compact torch design to allow for thermal spray application of coatings within confined components areas. cHVOF is a fully digitised process with different fuel sources allowing for the hybrid torch to acts as a HVOF or HVAF type process for maximum process flexibility offering improved coating hardness and retention of hard phases with tungsten carbide coating materials. Processing limits for internal diameters are coating material dependent but the smallest internal diameter for WC/Co is >90mm with up to 1m of insertion.
Materials (Broad Classification) – FeCrNiMo, FeCr, NiCr, NiAl, Self-Fluxing Ni alloys, MCrAlY, CoCrWBSi, CoCrNiW, CoCrWSiC, CoMoCrSi, Self-Fluxing Co alloys, Cu Alloys, Pure Molybdenum & Molybdenum alloys, Cr2C3/NiCr, WC/Co, other materials available upon request
Process Capacity
- The Castolin Eutectic workshop in Newcastle has four HVOF bays which can accommodate a wide variety of component sizes and geometries:
- Bay 1: XXXmm length x XXXmm OD x XXXKg (weight limit)
- Bay 1a: XXXmm length x XXXmm OD x XXXKg (weight limit)
- Bay 2: 7000mm length x 800mm OD x 3000Kg
- Bay 2a: XXXmm length x XXXmm OD x XXXKg (weight limit)
Special Considerations – The Castolin Eutectic workshop in Newcastle manufactures and applies specialist SealPlex™ and MoniPlex™ slurries, and other commercially available sealants as a method of coating densification to remove porosity and improve the corrosion resistance of as sprayed HVOF coating. HVOF is a replacement technology for hard chrome plating offering improved wear and corrosion resistance, coating uniformity and adhesion. The Castolin Eutectic workshop in Newcastle has the ability to strip old coatings to offer the potential for repair and overhaul of components.
Process Descriptor – Low Pressure Plasma Spray (LPPS) is a high temperature, low velocity plasma process which take place in a controlled atmosphere conditions to allow for oxidation sensitive materials including MCrAlYs & TBC materials to be sprayed onto components. The controlled atmosphere eliminates the formation of oxides within the coating and produces a high-quality coating including improved bond strength and coating density.
Materials (Broad Classification) – Abradables – AlSi Polyester, Al2O3, Al2O3/TiO2, Cr2O3, Cr2O3/TiO2, MCrAlY, NiCr, NiAl, WC/Co, TBC – ZrO2 XY2O3, Pure Molybdenum & Molybdenum alloys, Pure Si, Pure Ta, Pure Ti, TiC, TiO2, Y2O3, Self-Fluxing Ni alloys, Self-Fluxing Co alloys, other materials available upon request
Process Capacity
- Castolin Eutectic has two Air Plasma bays which can accommodate a wide variety of component sizes and geometries:
- MVC30: ___mm length x ___mm OD x 250Kg (weight limit)
Process Descriptor – The Castolin Eutectic workshop in Newcastle utilises a range of slurry coatings as a method of coating of complex components and as a method of thermal spray coating infiltration. MoniPlex® coatings are fully dense, pore free and exhibit very high hardness, adhesive strength and a low coefficient of friction. SealPlex® sealers are low viscosity and penetrate into the pores of thermal spray coating deposits to create a coating with improved ductility, improved fracture toughness and achieves improved surface texture. The Castolin Eutectic workshop in Newcastle slurry coatings are resistant to wear, corrosion, high temperature oxidation and other failure modes in extreme operational environments. The diverse range of MoniPlex and SealPlex material offer methods of combating failure in a range of different industries including Molten Metals, Oil & Gas and Steel. MoniPlex® and SealPlex® coatings are compatible with a range of different base materials including ferrous and non-ferrous alloys, including nickel alloys, titanium alloys, aluminium alloys, copper alloys, sintered ceramics and anodised aluminium films.
Materials (Broad Classification) – Proprietary inorganic slurries include:
- SealPlex® C1 – Pore free impregnation coating
- SealPlex® CP – Chemical barrier coating with electrical insultation coating with excellent release properties for molten tin and zinc
- MoniPlex® MX1 – excellent corrosion, wear and solid particle erosion resistance. Semi flexible coating resistant to thermal shock and stable at temperatures up to 2000oC.
- MoniPlex® MAC1 – High temperature oxidation resistance. Low friction – high lubricity factor, good sliding wear resistance and thermal shock resistance.
- MoniPlex® MB – Tough, wear resistant surface – superb abrasion and erosion resistance. Excellent resistance to molten materials impermeable barrier coating
- Other slurries, sealant and paint systems available upon request including Ipcote materials and molybdenum disulphide
Process Capacity
- Component size is limited by furnace capacity for furnace cured inorganic slurries, but air cured materials are available which do not require furnace heat treatment:
- Rotor Oven - ___mm length x ___mm OD x ___Kg (weight limit)
- Box Oven - ___mm length x ___mm OD x ___Kg (weight limit)
- Component Kiln Oven - ___mm length x ___mm OD x ___Kg (weight limit)
Special Considerations – Component geometry is not a limiting facture for the application of MoniPlex® slurry coatings due to high fluidity of the pre applied coating, with the ability to coat internal diameters as small as 0.5mm.
Process Descriptor – The Castolin Eutectic workshop in Newcastle offers total manufacture of components to print with abrasion, corrosion, erosion and temperature resistant coatings including the application of MoniPlex® or SealPlex® slurries and sealants to fully seal and densify thermal spray coatings, including pre and post machining. Where additional operations are required outside of coating, slurry, heat treatment and machining operations, The Castolin Eutectic workshop in Newcastle will source this capability as a part of the scope of work.
Materials (Broad Classification) – The Castolin Eutectic workshop in Newcastle is able to manufacture components across a range of different substrates and coating materials:
- Base Materials: Ferrous (Carbon Steel, Alloy Steel, Stainless Steel, Duplex Steel, Super Duplex Steel) and non-ferrous alloys (Inconel, Monel, Hastelloy, Incoloy, Stellite, Bronze & Copper Alloys)
- Coating Materials: As defined on coating pages (HVOF, Plasma, Arc Spray, Flame Spray)
- Other base and coating materials available upon request
Process Capacity
- Castolin Eutectic are limited by furnace, but air cured materials are available which do not require furnace heat treatment:
- CNC: XXXmm length x XXXmm OD x XXXKg (weight limit)
- Grinding: XXXmm length x XXXmm OD x XXXKg (weight limit)
For components that size outside of this range, The Castolin Eutectic workshop in Newcastle will source relevant capability to support component manufacture
Special Considerations – Depending on the type of coating application method defined during manufacture, the nature of the machining operations will need to be considered. Castolin Eutectic will support in defining the correct operational sequences require to successfully produce the finished component.
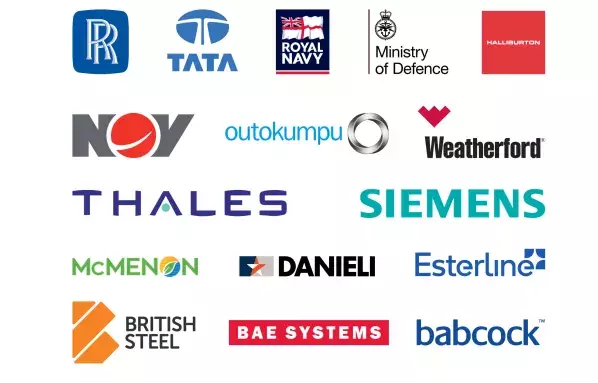
Global customer endorsements
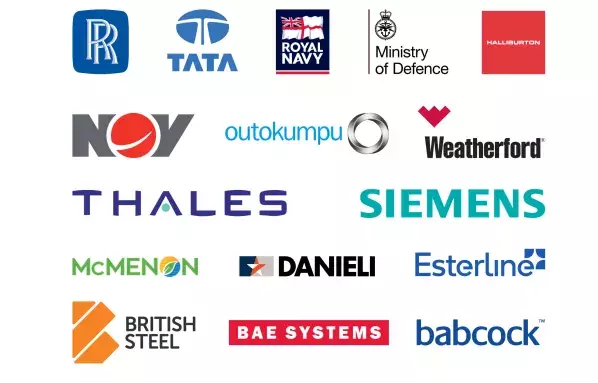
Rolls-Royce, Halliburton, TATA, Siemens, BAE Systems, Babcock, Thales, Ministry of Defence, British Royal Navy, Weatherford, Danieli, British Steel, Esterline, Total Steel Production, McMenon, Outokumpu, National Oilwell Varco
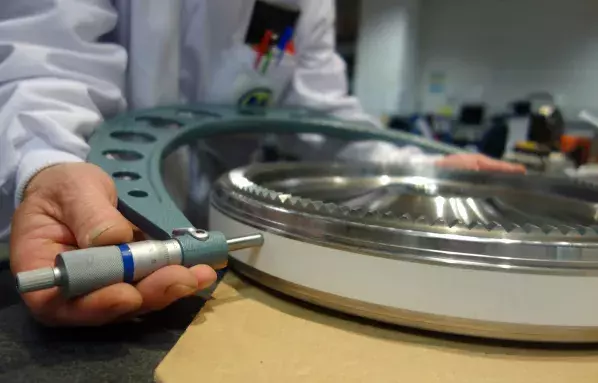
Laboratory facilities: inspection, analysis, and testing services
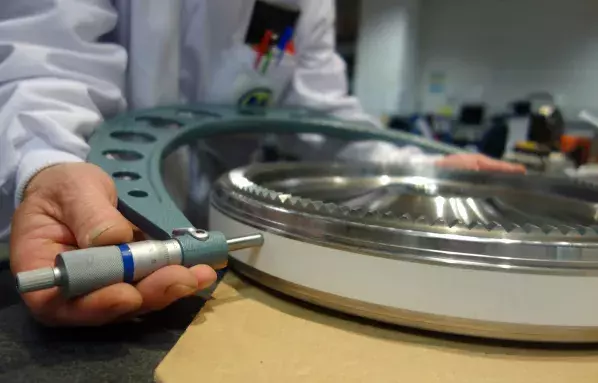
The laboratory’s facilities include:
- Visual inspection, Dimensional inspection, Non Destructive Inspection, Dye penetrant, Surface Roughness Testing, Sample preparation, Mounting – cold cure and vacuum, Grinding, Polishing
- Micrographic analysis
-- Porosity, Interfacial contamination
-- Micro cracks/cracking, Oxides, Un-melts, Carbide content,
- Hardness Testing, Macro Hardness Rockwell, Micro Vickers Hardness
- Adhesion Testing Pull Test, Bend Test, Salt spray (fog) testing
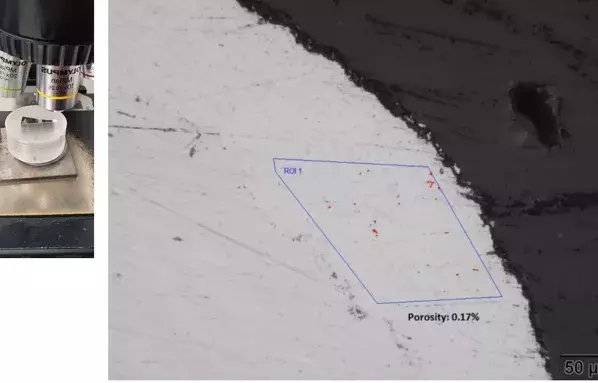
Advanced laboratory services
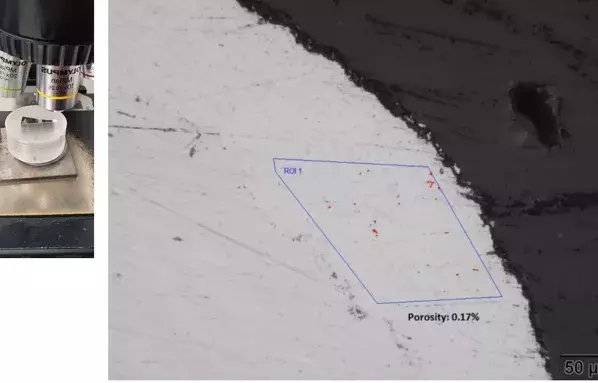
The laboratory’s facilities include:
- Visual inspection
- Dimensional inspection
- Non Destructive Inspection
- Dye penetrant
- Surface Roughness Testing
- Sample preparation
- Mounting – cold cure and
- vacuum
- Grinding
- Polishing
- Micrographic analysis -- Porosity
-- Interfacial contamination -- Micro cracks/cracking
-- Oxides -- Un-melts -- Carbide content
- Hardness Testing -- Macro Hardness Rockwell
-- Micro Vickers Hardness
- Adhesion Testing
- Pull Test
- Bend Test
- Salt spray (fog) testing
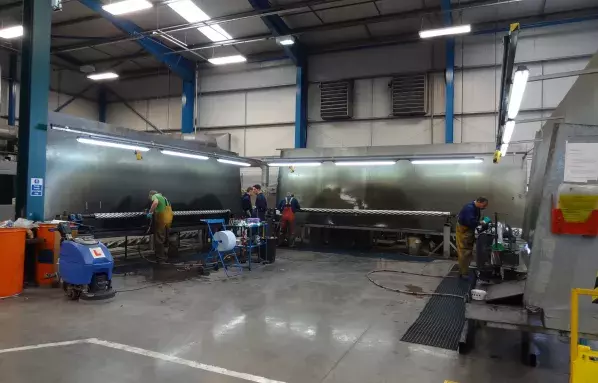
Advanced capabilities showcased in our workshop
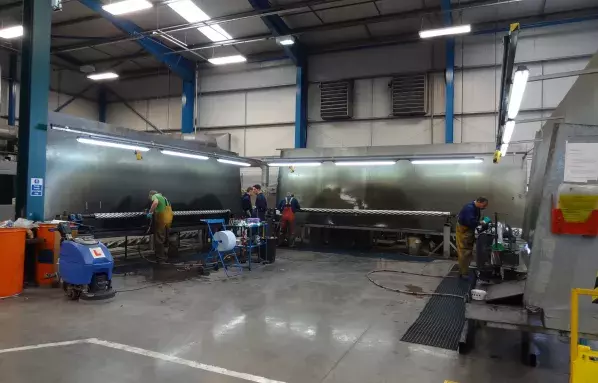
- Vapour Degreaser
- Abrasive Blasting
-- 2 x Euro 7» blast cabinets
-- 2 x Euro 10» blast cabinets
-- 1 blast room with maximum component size of 7m in length
- Flame Spray
- Twin Arc Spray
-- 1.6mm and 2.3mm wires
-- Offsite and Onsite capability available
- Plasma – 2 x booths
-- Controlled by ABB
-- 1 x booth operating Metco 7m gun
-- 1 x booth operating Metco 3m gun
- High Velocity Oxygen Fuel – 2 x booths
-- Booth 1 controlled JP5000 gun and 8000 console.
- Maximum component size of 1.5m height and 2.9m in length
-- Booth 2 robotically controlled by ABB Robot with 30kg capacity, with a JP5000 gun and
- Metco console. Maximum component length of 7m
- Low Pressure Vacuum Plasma
-- Turntable capable of spraying rings
- Box Oven and Kiln
-- 320 Degrees Celsius Maximum
- Diamond polishing of Mud Rotors
- LPPS Chambe
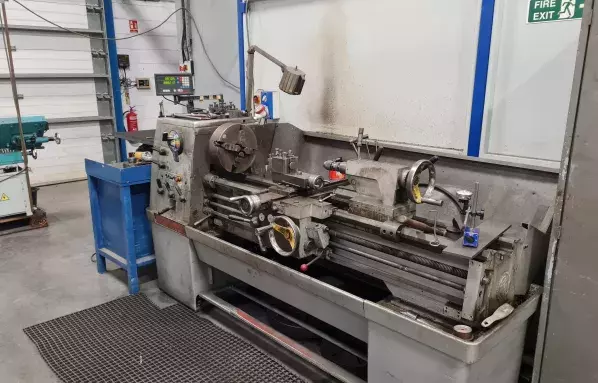
Aerospace-certified machine shop equipped for critical parts
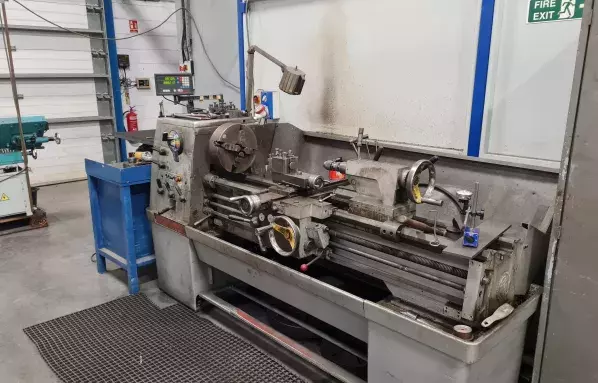
Small machine shop approved to complete aerospace critical parts. The machine shop’s facilities include:
- External CNC lathe
- External CNC grinder
- Complex parts 5 axis machining
- Inner diameter and outer diameter surfaces
- TIG/MIG welding
- Including Plasma Transferred TIG/MIG
- Pillar drill
- Colchester lathe