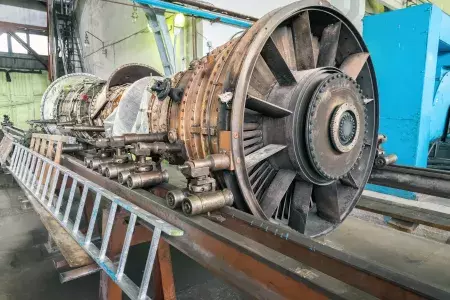
Thermal Barrier coatings
Thermal barrier coatings (TBC's) are widely used in the hot sections of gas turbines to enhance the life of combustors, vaporisers, nozzle guide vanes, etc which are exposed to high temperature oxidation and sulphication attack.
Thermal Barrier coatings are normally applied to the platform surfaces of nozzle guide vanes as shown here and a typical coating specification would be an MCrAIY bond coat deposited by Low Pressure Plasma Spraying (LPPS) and a top coat of zirconia partially stabilized with yttrian deposited in air by Robotic Plasma Spraying.
Thermal Barrier Coatings provide protection to metallic component operating in extreme environments including aerospace and industrial gas turbines, power generation and marine propulsion systems. The most common Thermal Barrier Coatings consist of a ceramic topcoat (typically yttria stabilised zirconia) and an oxidation resistant metallic MCrAlY bond coat to create a thermal gradient between the coating and the component to improve mechanical characteristics of the base material and allow the component to operate at higher and higher temperatures to improve the efficiency of the turbine. Thermal barrier coatings also protect critical components against erosion, corrosion and foreign object damage when in service. The Castolin Eutectic Workshop in Newcastle is approved to apply a range of thermal barrier coatings (bond coat and topcoat) for aerospace and industrial gas turbines.
Description
Thermal barrier coatings (TBC's) are widely used in the hot sections of gas turbines to enhance the life of combustors, vaporisers, nozzle guide vanes, etc which are exposed to high temperature oxidation and sulphication attack.
Thermal Barrier coatings are normally applied to the platform surfaces of nozzle guide vanes as shown here and a typical coating specification would be an MCrAIY bond coat deposited by Low Pressure Plasma Spraying (LPPS) and a top coat of zirconia partially stabilized with yttrian deposited in air by Robotic Plasma Spraying.
Thermal Barrier Coatings provide protection to metallic component operating in extreme environments including aerospace and industrial gas turbines, power generation and marine propulsion systems. The most common Thermal Barrier Coatings consist of a ceramic topcoat (typically yttria stabilised zirconia) and an oxidation resistant metallic MCrAlY bond coat to create a thermal gradient between the coating and the component to improve mechanical characteristics of the base material and allow the component to operate at higher and higher temperatures to improve the efficiency of the turbine. Thermal barrier coatings also protect critical components against erosion, corrosion and foreign object damage when in service. The Castolin Eutectic Workshop in Newcastle is approved to apply a range of thermal barrier coatings (bond coat and topcoat) for aerospace and industrial gas turbines.
Applications
Thermal Barrier Applications for Aerospace & Industrial Gas Turbine:
- Blades
- Combustion Chambers
- Cooling Rings
- Heat Shields
- Interconnectors
- Shrouds
- Transition Ducts
- Throat Rings
- Vanes
- Vaporiser Tubes