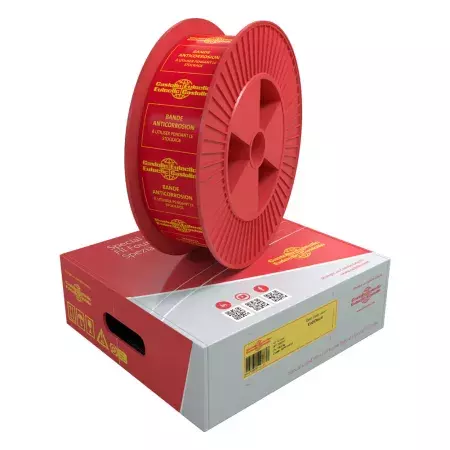
CaviTec GMA
Uniquely Engineered Electrodes and Wires Designed to Resist Severe Cavitation-Erosion Damage
A patented, proprietary alloy uniquely engineered to resist damage from severe cavitation-erosion, CaviTec is manufactured under license from Hydro-Quebec-Canada. CaviTec, with its enhanced properties, is an austenitic-type alloy containing controlled amounts of chromium, cobalt, silicon and maganese. The finely con-trolled balance of these elements significantly improves strain-hardening and shock-dampening properties. The result: improved cavitation-erosion resistance.
CaviTec is proven to last up to six times longer than traditional stainless steel overlays. This high strain, work-hardening austenitic stainless steel delivers max-imum protection for areas needing frequent or major repairs. CaviTec’s all position weldability also makes controlled overlapping and profiling very easy to do. Essentially an austenitic γ-phase structure. This met-astable phase transforms under cyclical stress to an α-martensitic phase which results in a very fine defor-mation twinning.
Recommended welding procedure:
Preparation: Remove damaged area with arc-air or plas-ma gouging. Grind gouged surface to remove oxides and slag. Minimum depth of preparation should be 3,2 mm or 1/8”. If the refill depth is greater than 9,5 mm or 3/8” first fill with a grade 309L. This preparation is need-ed to maintain a maximum CaviTec deposit depth of 9,5 mm or 3/8”.
Technique: Maintain a medium-to-short arc and incline the electrode at a 45° angle in the direction of travel. The preferred bead profile should be a non-weave. Back-fill craters to reduce crater-cracking tendencies.
Post-welding: Grind to profile.
(* In highly stressed regions of the turbine runner it is recom-mended that a buttering layer of 309L be deposited. In such cases, the minimum depth of preparation should be increased to 1/4“ (6mm).)
Technique: Maintain a medium-to-short arc and incline the electrode at a 45° angle in the direction of travel. The preferred bead profile should be a non-weave. Back-fill craters to reduce crater-cracking tendencies.
Post-welding: Grind to profile.
(* In highly stressed regions of the turbine runner it is recom-mended that a buttering layer of 309L be deposited. In such cases, the minimum depth of preparation should be increased to 1/4“ (6mm).)
Description
A patented, proprietary alloy uniquely engineered to resist damage from severe cavitation-erosion, CaviTec is manufactured under license from Hydro-Quebec-Canada. CaviTec, with its enhanced properties, is an austenitic-type alloy containing controlled amounts of chromium, cobalt, silicon and maganese. The finely con-trolled balance of these elements significantly improves strain-hardening and shock-dampening properties. The result: improved cavitation-erosion resistance.
CaviTec is proven to last up to six times longer than traditional stainless steel overlays. This high strain, work-hardening austenitic stainless steel delivers max-imum protection for areas needing frequent or major repairs. CaviTec’s all position weldability also makes controlled overlapping and profiling very easy to do. Essentially an austenitic γ-phase structure. This met-astable phase transforms under cyclical stress to an α-martensitic phase which results in a very fine defor-mation twinning.
Recommended welding procedure:
Preparation: Remove damaged area with arc-air or plas-ma gouging. Grind gouged surface to remove oxides and slag. Minimum depth of preparation should be 3,2 mm or 1/8”. If the refill depth is greater than 9,5 mm or 3/8” first fill with a grade 309L. This preparation is need-ed to maintain a maximum CaviTec deposit depth of 9,5 mm or 3/8”.
Technique: Maintain a medium-to-short arc and incline the electrode at a 45° angle in the direction of travel. The preferred bead profile should be a non-weave. Back-fill craters to reduce crater-cracking tendencies.
Post-welding: Grind to profile.
(* In highly stressed regions of the turbine runner it is recom-mended that a buttering layer of 309L be deposited. In such cases, the minimum depth of preparation should be increased to 1/4“ (6mm).)
Technique: Maintain a medium-to-short arc and incline the electrode at a 45° angle in the direction of travel. The preferred bead profile should be a non-weave. Back-fill craters to reduce crater-cracking tendencies.
Post-welding: Grind to profile.
(* In highly stressed regions of the turbine runner it is recom-mended that a buttering layer of 309L be deposited. In such cases, the minimum depth of preparation should be increased to 1/4“ (6mm).)
Applications
- Francis turbines
- Kaplan turbines
- Propeller turbines
- Bulb turbines
- Draft tubes
- Impellers
- Pumps & valves
- Wicket gates
Technical Data
Typical Hardness (as deposited)
250 - 280 HV30
Typical Hardness (work-hardened)
270 - 300 HV30
Typical Hardness
230-260 - 308/309 stainless steel
Castolin Eutectic