Vertical Roller Mill Refurbishment: "Speed and Reliability are critical"
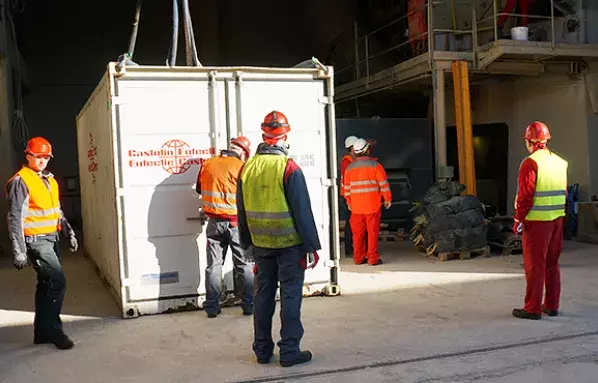
At the beginning of May 2014, the Castolin Eutectic mobile intervention team performed a vertical roller mill (VRM) refurbishment operation in a cement plant in Switzerland. Martin Trenk, worldwide VRM Business Unit Manager, was present on-site and explained the vertical roller mill wear problem and the Castolin Eutectic approach for a fast and long-lasting repair.
1. What wear phenomenon intervenes for this Vertical Roller Mill (VRM) and what are the consequences for the functioning of the plant?
A cement mill is a “continuous process“ plant. One process depends on the other. When you manufacture cement, various raw materials are used, such as natural and synthetic minerals, so there has to be a very smooth and continuous feed of the raw material. The VRM has the function of grinding this raw material and feeding it for further processing – it has a key function. When it stops, then the most expensive part of the cement plant, the kiln, gets affected. That is why running the VRM continuously, without any trouble, is key to the successful functioning of the further operations for cement manufacturing and energy conservation in the whole process.
2. How can Castolin Eutectic help solve the VRM wear problem?
Cement plants always work under time pressure especially when it comes to shutdowns. Everybody wants the shutdown to be limited to a short maintenance operations period, so you have to complete the job to the customer satisfaction within the available time. And most of the conventional processes do not allow that. This is tricky in maintenance repair – you don’t know what to expect before you actually carried out the job. So shutdowns require very efficient time management to repair a big mass of components that a cement plant usually has. So it’s not only the speed of the repair but also the reliability of the repair, which are critical. And with the Castolin Eutectic process and automation system, which allows welding of rollersand table simultaneously, the customer benefits of an optimum solution. He achieves a speedy repair, but most importantly, a more reliable and in case of welding quality repeatable repair than he was getting before.
3. How many kgs of metal will be deposited for the VRM refurbishment?
For this VRM repair job, about 1.6 tons (1.600 kgs) are needed to achieve the requested roller profile. The deposition rate always depends on the type of mill, the needed welding material and the number of torches we can use at the same time. Castolin has developed different special solutions to get optimal deposition rates for each type of mill.
4. How many days will the Vertical Roller Mill refurbishment operation take?
This job will be finished within 5 days including setup and dismantling of the equipment. Especially for this Pfeiffer mill the main advantage for the customer assisted by the Castolin VRM Service Team is that he doesn’t need to take out the rollers for re-welding or organise expensive scaffoldings.
5. How will the Castolin solution prolong the wear life of the VRM?
The customer is spending for downtime on an hourly basis. In a cement plant, the loss is always a couple of hundreds of thousands euros per hour. Field experience, together with R&D and our advanced welding wire manufacturing plant in Ireland, allows our VRM team to develop special anti-wear products and leading-edge welding processes. Castolin makes no compromises in case of torch arrangement inside the mill to achieve the best welding quality possible resulting in longer service life of the welded sections compared to the original casted material.