Did you know Castolin Eutectic launched an e-commerce site https://shop.castolin.com?
Deliveries are currently only to UK, Ireland, Germany, Austria and Romania. Here's a discount code for your first online purchase: RABATT10
Enjoy!
Choose a category
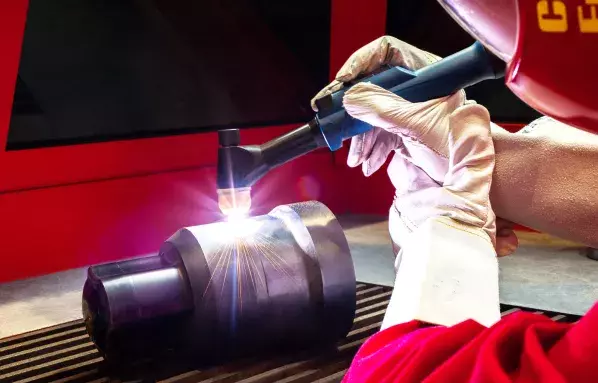
Lowest dilution, heat input, distortions
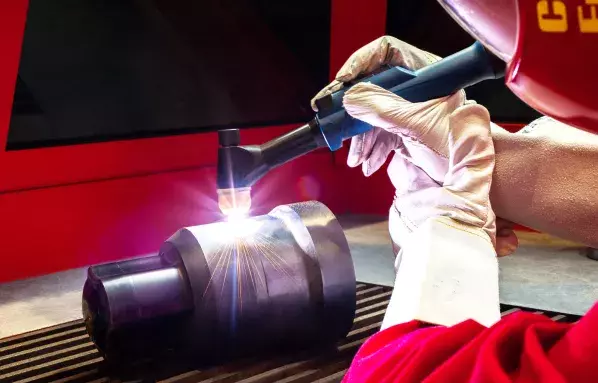
Minimal dilution of the base material, readily automated, easily controlled welding bead means for you high quality and wear resistant coatings in a wide variety of alloys. Excellent for series production. In the PTA process, the plasma is focused while forced through the heat resistant anode, causing a considerable increase of the arc density, energy and temperature. The welding filler alloy, in microatomised powder or cold wire form, is conveyed into the plasma arc column where a shielding gas protects the weld pool from the atmosphere. Castolin has developed special powders for GAP applications supported by a complete high-quality GAP equipment range.
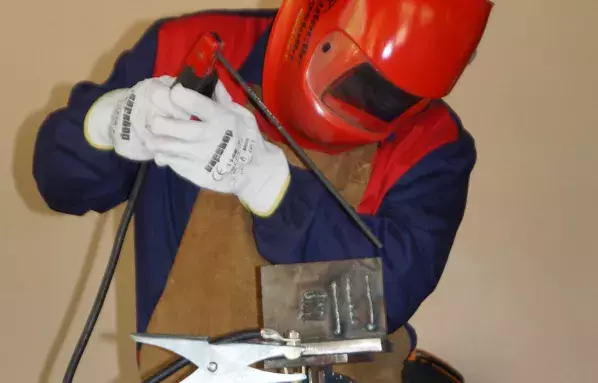
Effective even underwater or on windy, stormy weather
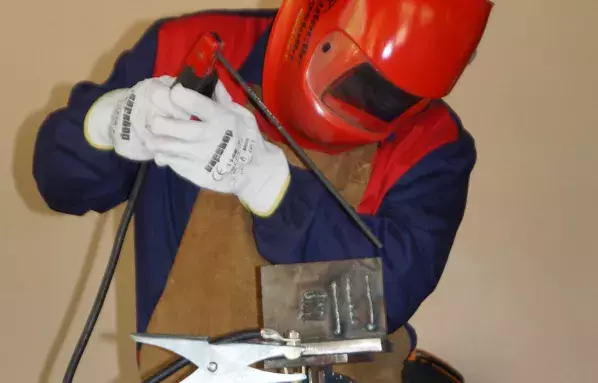
When an arc is struck between the flux coated electrode and the workpiece, both the core wire and the workpiece surface melt to form a weld pool. Simultaneous melting of the flux coating on the rod will form gas and slag which protects the weld pool from the surrounding atmosphere. The slag will solidify and cool and must be chipped off the weld bead once the weld run is complete (or before the next weld pass deposit). Castolin has developed the special EutecTrode® alloy range of low heat input electrodes for industrial wearfacing, repair and joining applications supported by a complete high quality, MMA welding equipment range based on latest technology.
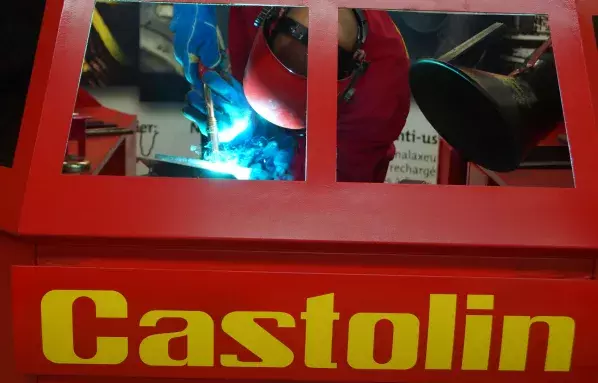
Clean, efficient and easy to learn
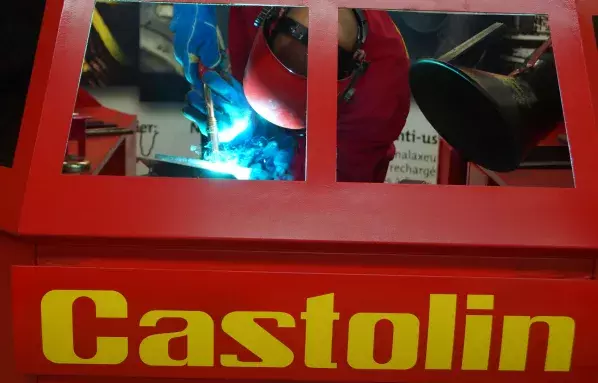
MIG is similar to MMA in that heat is produced by forming an arc between a metal electrode and the workpiece. The electrode melts to form the bead. The main differences are that the metal electrode is a small diameter wire fed from a spool and an externally supplied shielding gas is necessary. As the wire is continuously fed, the process is often referred to as semi-automatic welding. The pulse mode was developed as a means of stabilizing the arc at low current values below the threshold level, to avoid short-circuiting and spatter. Metal transfer is achieved by applying pulses of current, each pulse having sufficient force to detach a droplet. Castolin has developed the special EnDOtec® (cored wire) and CastoMag® (solid wire) alloy ranges for industrial wearfacing, repair and joining applications supported by a complete high quality, MIG / MAG welding equipment range based on latest technology.
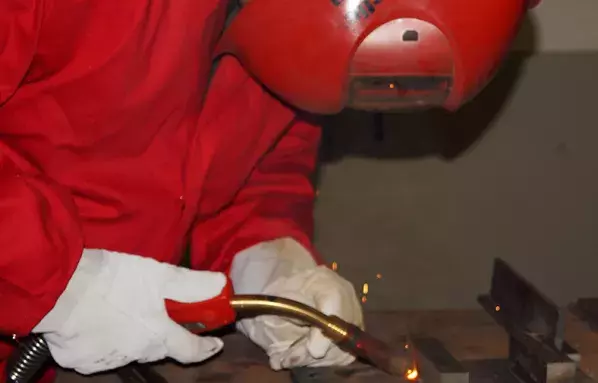
High quality deposits at great speed
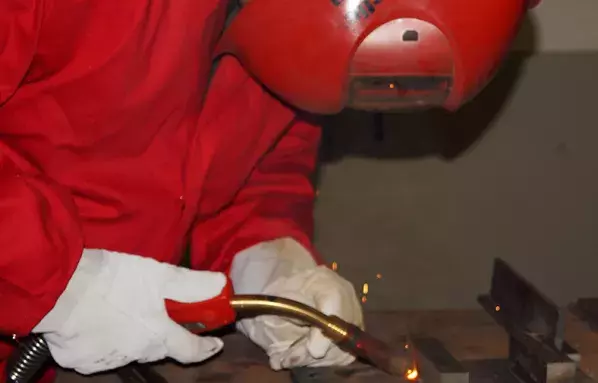
Open arc continuous electrodes consist of an outer strip of special alloy, the core of which is packed with a high density of micro-elements. The design makes it possible to obtain high quality deposits at great speed, for coating resistant to all types of wear, as well as for joining. Within this technology a variety of alloys of different formulation can be produced. Castolin Eutectic has developed the special self-shielded TeroMatec® (flux cored wire) alloy range of low heat input electrodes and the TeroMatec 400 wire feeder for industrial wearfacing, repair and joining applications.
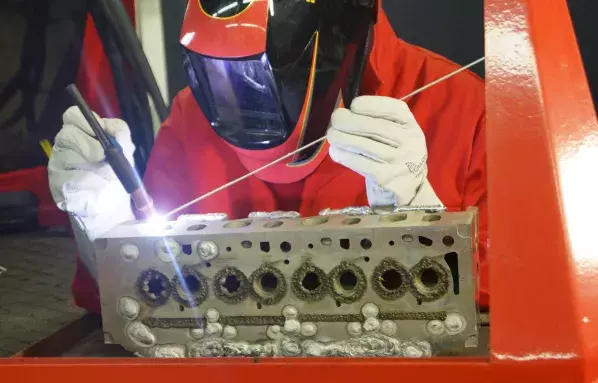
A high degree of operator skill required
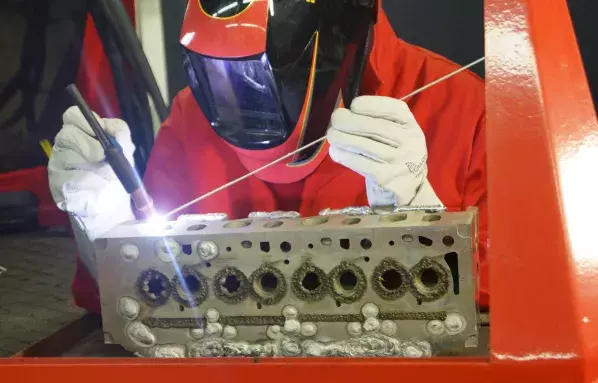
In the TIG process the arc is formed between a pointed tungsten electrode and the workpiece in an inert atmosphere of argon or helium. The small intense arc provided by the pointed electrode is ideal for high quality and precision welding. As the tungsten electrode is not consumed during welding, the heat of the arc will melt the base metal and a separate filler rod can be added into the weld pool if required. Castolin has developed the special CastoTig® alloy range for industrial wearfacing, repair and joining applications supported by a complete CastoTIG® welding equipment range based on latest technology.
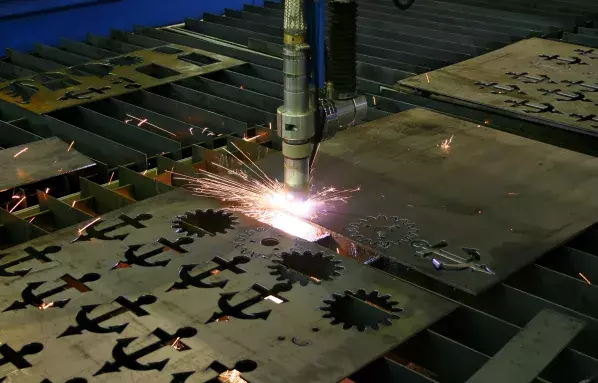
A cost-effective technology
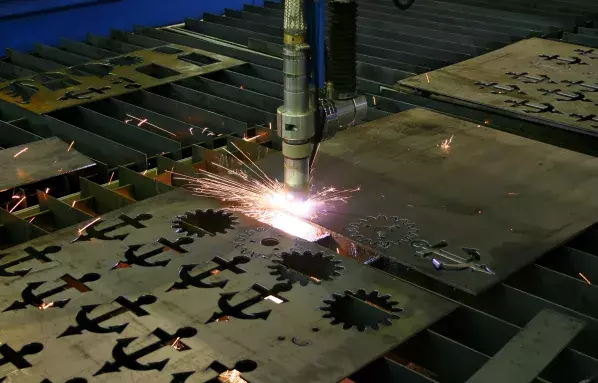
Plasma cutting has always been seen as an alternative to the oxy-fuel process. However, the important difference between the two processes is that while the oxygen-fuel process oxidises the metal and the heat from the exothermic reaction melts the metal, the plasma process operates by using the heat from the arc to melt the metal. The ability to melt the metal without oxidation is essential when cutting metals, such as stainless steel, which form high temperatures oxides. Plasma is an effective means of cutting thin and thick materials alike. Handheld torches can usually cut up to 2 in (48mm) thick steel plate, and more powerful computer-controlled torches can pierce and cut steel up to 12 inches (300mm) thick. Castolin Eutectic has developed a complete high-quality Plasma cutting equipment range called AirJet based on the latest technology.
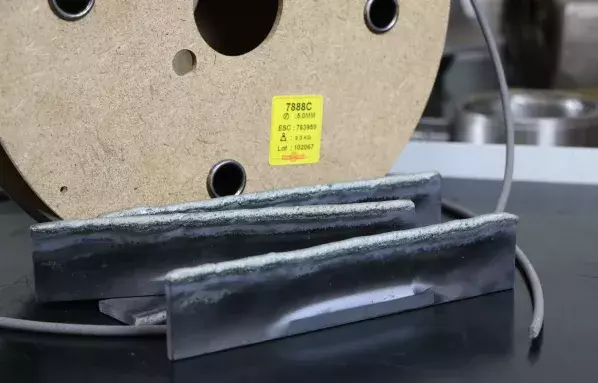
innovative low temperature hardfacing
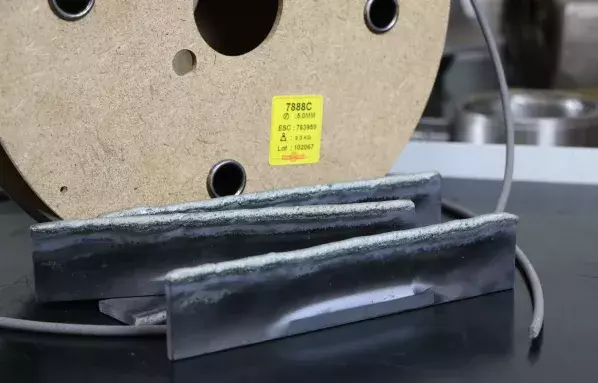
Deposition of diverse alloys and composite materials, using readily available flame equipment, means most abrasion resistant coatings applied with optimal metallurgical bonding and zero dilution with the base material.
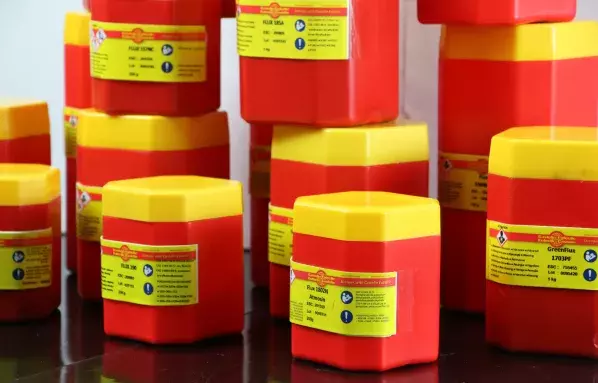
For cleaning, wetting and protection
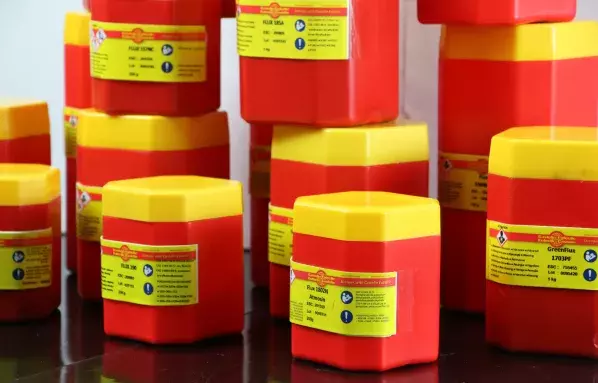
Fluxes are carefully engineered chemical products used for removing metal oxides from the surface of metal parts to be joined. This removal or cleaning process takes place during the brazing operation. The selection of the optimal flux for the application, base metal and brazing alloy is essential for successful brazing operations.
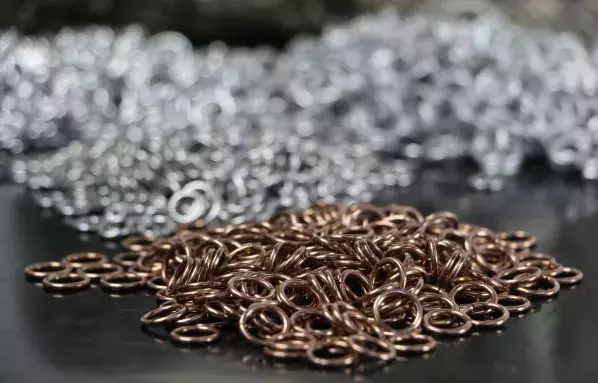
We produce solid rings and tailor-made rings with inner flux
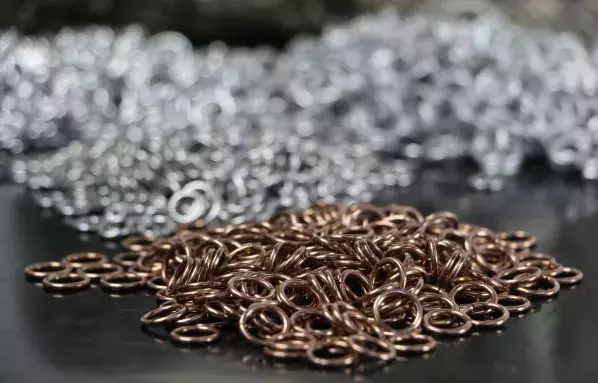
Our vast product range includes a wide selection of filler metals in the form of diverse rings, foils, wires, rods, pastes and special pre-forms to meet all your OEM and maintenance requirements.
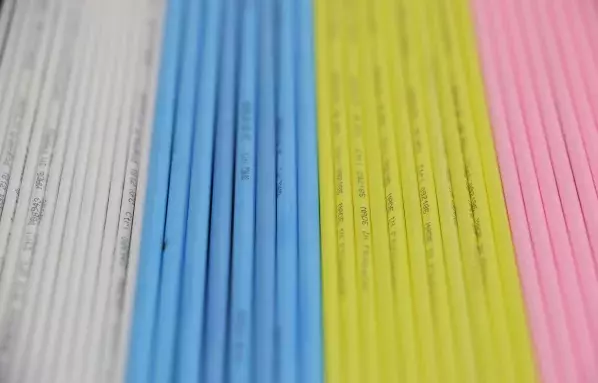
Optimal ratio of flux and metal for all standard jobs
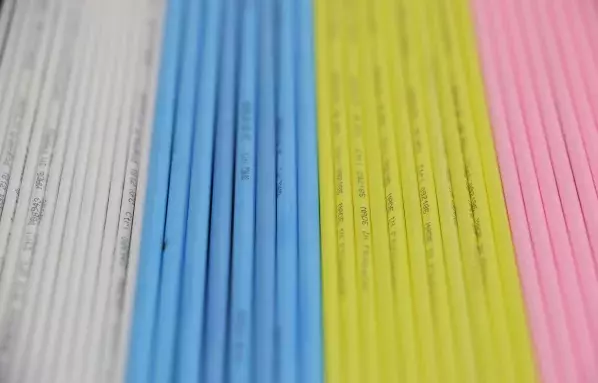
At Castolin Eutectic, we understand that each application has individual and specific requirements. Therefore, we have designed and manufactured several types of coated rods to meet the demands of our customers. Unlike most competitors, we do not use a universal flux for all rods, each rod contains the type of flux required by the alloy being coated. Additionally, each alloy has a specific flux coating colour which helps operators know which alloy/colour to use.
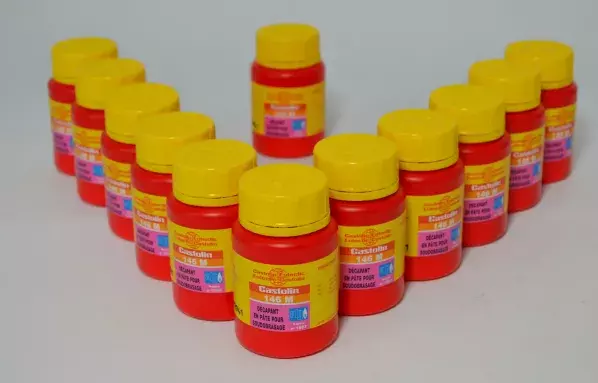
Reduce filler metal consumption
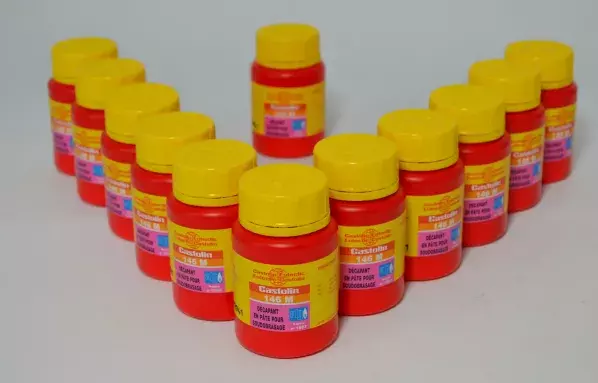
Brazing pastes are the best choice for automated processes. Castolin Eutectic's pastes distinguish themselves from the competition by having:
- Maximum paste stability
- Optimised dispensing characteristics
- Easy clean-up with water (hands, tools)
- Minimum development of smoke (furnace brazing)
- Binder does not influence the brazing process
- Maximum capillarity
- Highest quality metal powder
- Simple flux residue removal
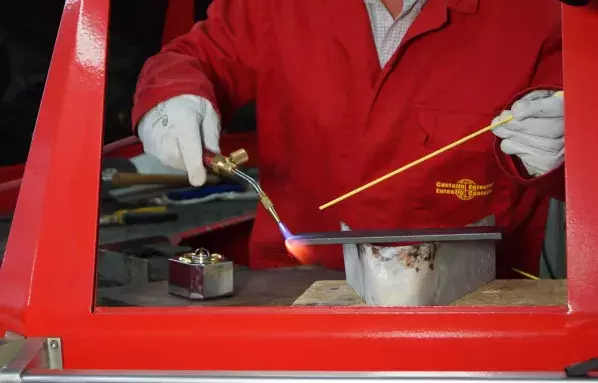
Brazing can be used on dissimilar metals and materials
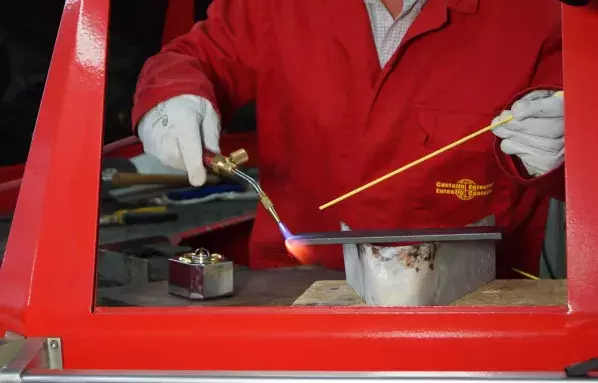
Brazing has been around for 1000s of years. Brazed joints have been used in plumbing, air-conditioning, heating, electronics and numerous other applications for a very long time. A brazed joint will last a lifetime and is proven to do so. Other materials, such as plastic, have not been around long enough to make the same claims. Additionally, if you do not get it right the first time, with brazing you can reheat the joining and repair it without having to disassemble, or completely reinstall the affected parts. You can rest assure that when brazing you are using the most reliable joining solution on the market.
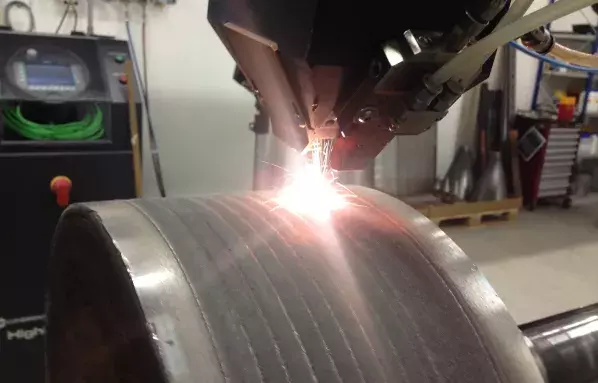
Part distortion is avoided
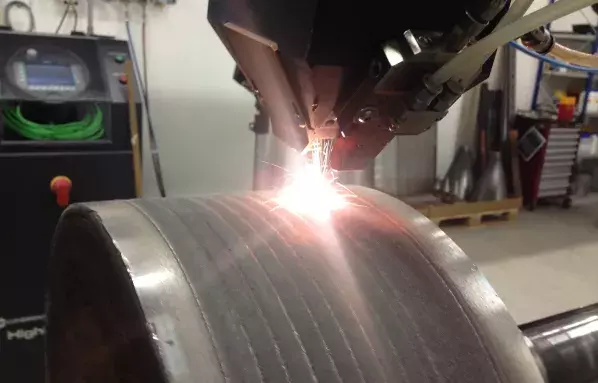
The arrival of High Power Direct Diode (HPDD) laser technology a few years ago started to drastically change the landscape of hardfacing. The HPDD technology was able to maintain its high power efficiency and quality, whilst dramatically reducing the cladding time and cost. With the introduction of the first 8KW HPDD laser in Europe by Castolin Eutectic, the full advantages of this breakthrough can now be exploited. To date, 4 diode LaserClad units are installed within Castolin Eutectic premises globally. Our offer includes laser coating serices (deposition of thick coatings on large parts, precision cladding with thin coatings on small parts, repair and maintainence of industrial parts, R&D support for novel materials), manufacturing of Laser Cladding powders and fully automated and integrated laser cladding facilities.
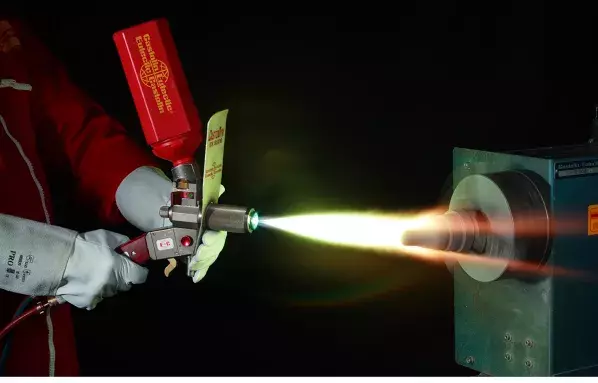
Low level of noise and fumes
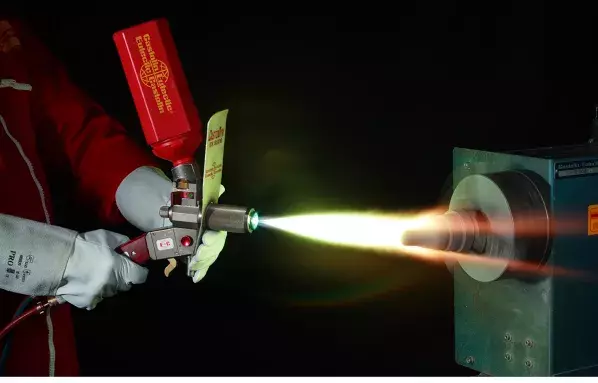
Minimum thermal input, good bonding achieved with substrate material, and wide range of alloys mean cost-effective coating solutions for a wide range of wear problems.
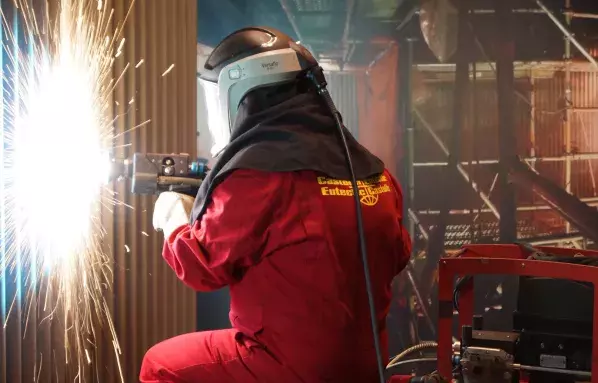
Highest productivity thermal spraying process
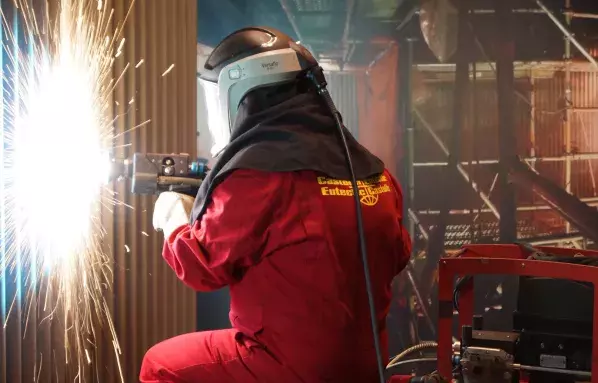
High deposition rates achieved using electrical arc melting of two cored or solid wires simultaneously means high-quality alloy coatings achieved at affordable prices. On-site spraying for large surfaces.
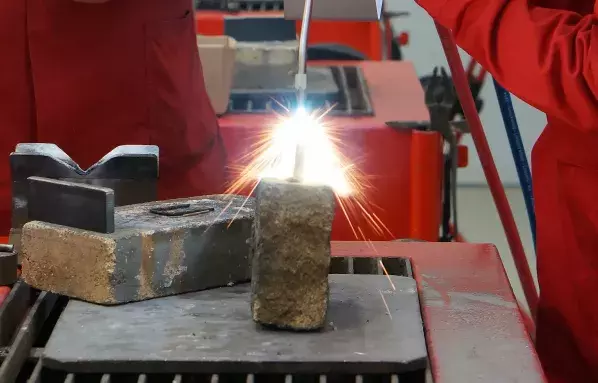
Homogeneous and pore-free coatings
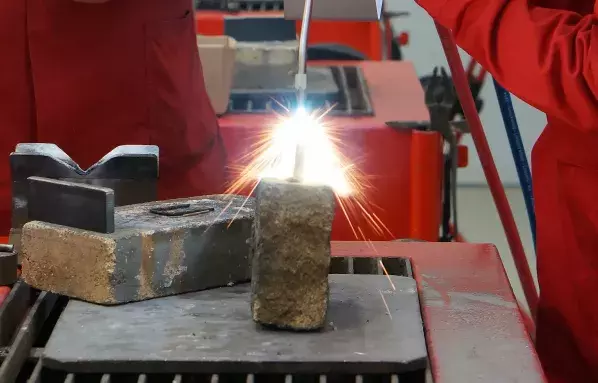
Subsequent fusing gives true metallurgical bonding and a fully dense coating. This means optimum coating quality, excellent for severe abrasion, corrosion and oxidation.
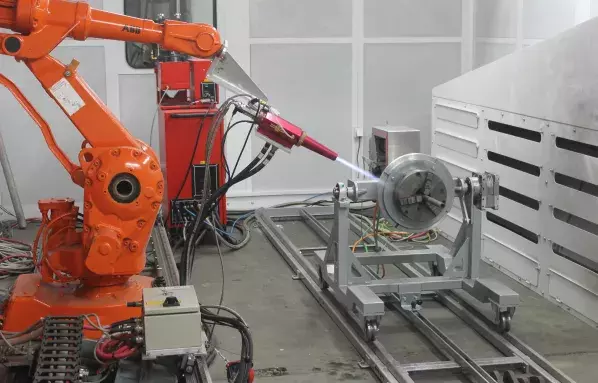
Repeatable coating quality
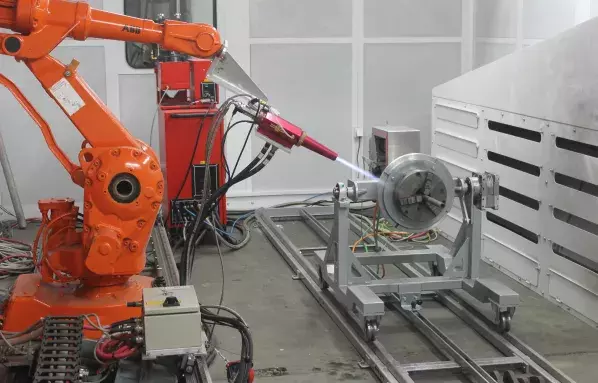
Cold spray process at supersonic particle speeds for maximum mechanical bonding means aeronautic quality coatings available at industrial prices, variety of materials and superhead carbides can be applied in thin layers.
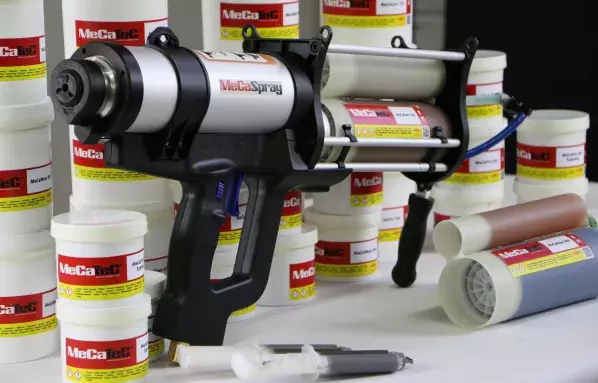
Perfect balance between affordability & performance
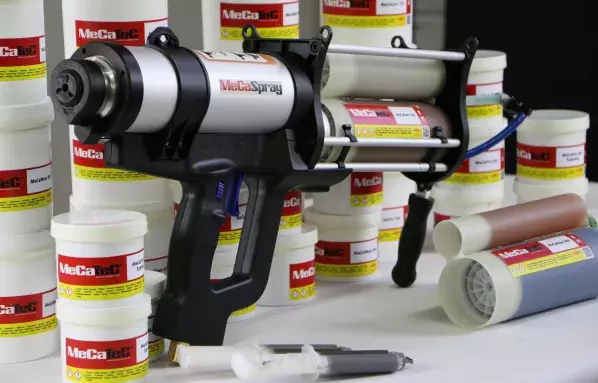
Two-component products applied at ambient temperature means no thermal distortion of parts, very rapid and easy procedures. Protection for unweldable parts and/or complex geometry.
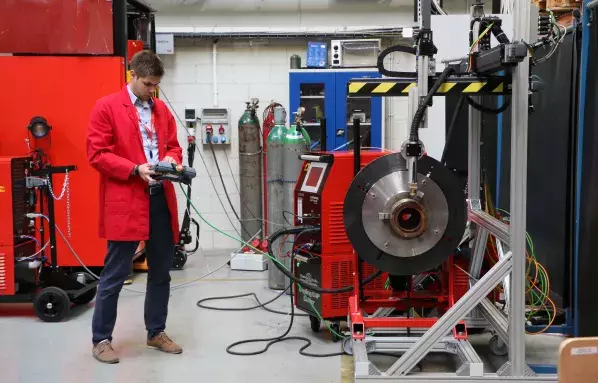
For maximum customization
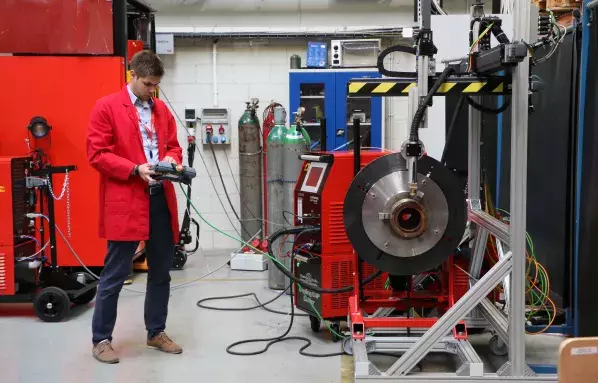
Castolin Eutectic has designed, manufactured and commissioned many Turnkey Integrated Systems on a global basis. We have serviced several industries and applications with tailored made system solutions that are fully engineered, cost efficient, flexible and have state of the art safe operating features. Typical designs include control equipment, sound-proof cabins, robots, turn tables, extraction, etc. These components are fully integrated for operation in automatic mode. As well as providing full monitoring with operational status and alarms, the systems also allow manual intervention for further development and optimisation of parameters.
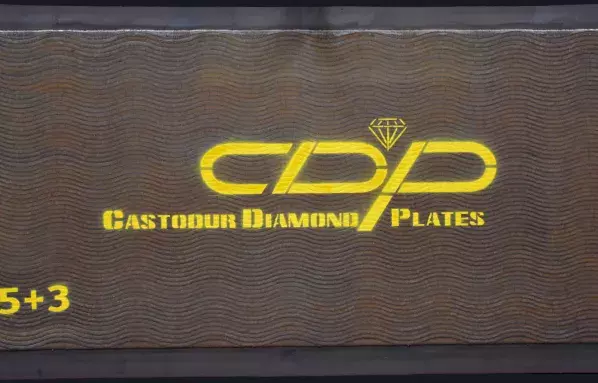
Increase plant availability
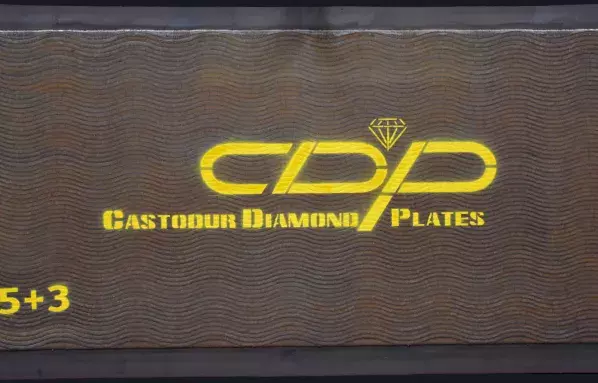
With more than 100 years experience in welding and wear protection, Castolin Eutectic is the manufacturer of the widest range of wearplates today on the market in terms of base materials, sizes, coating alloys, and welding processes adopted. From simple Chromium Carbide rich overlays, applied in open arc, to sophisticated NiCrBSi powders additioned with Tungsten Carbides and fused in a vacuum furnace or by means of Plasma Transferred Arc, we have developed a wide choice of products.
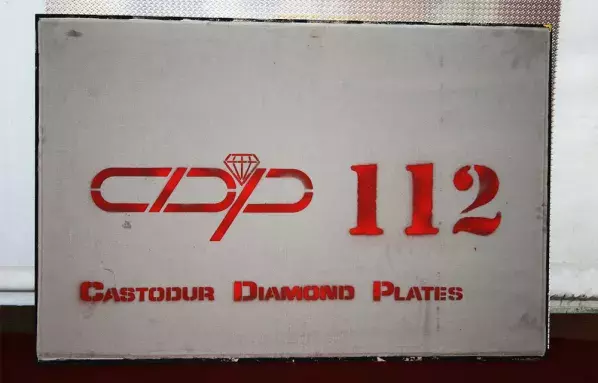
High value surface structure with excellent flatness
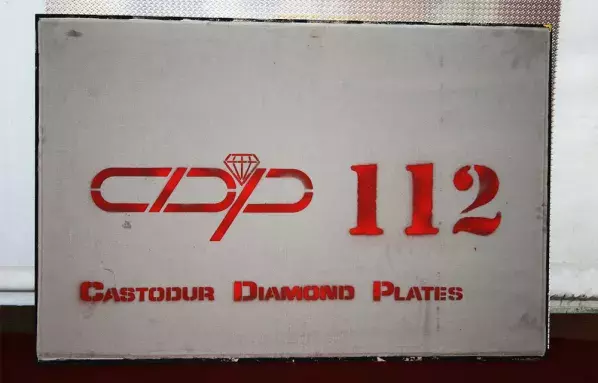
CDP® Powder Plates are produced by overlaying an easy-to-weld steel plate with a metal powder alloy fused in a furnace under protected atmosphere. The main advantage of these products is the 100% dilution-free overlay obtained, that ensures maximum protection even with just a few millimetres of deposit thickness. Lightweight and therefore easy to handle. Easily formed, and therefore also suitable to tight bending radius.
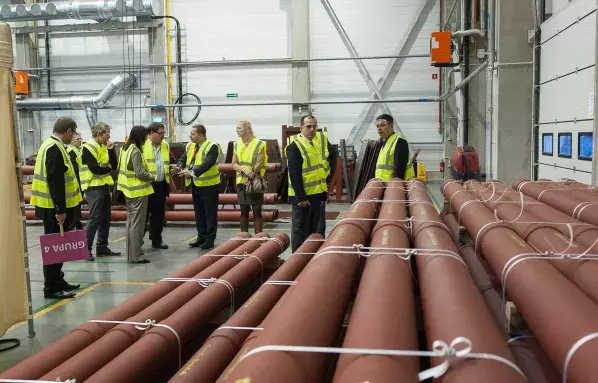
Custom cutting, elbows and joints available
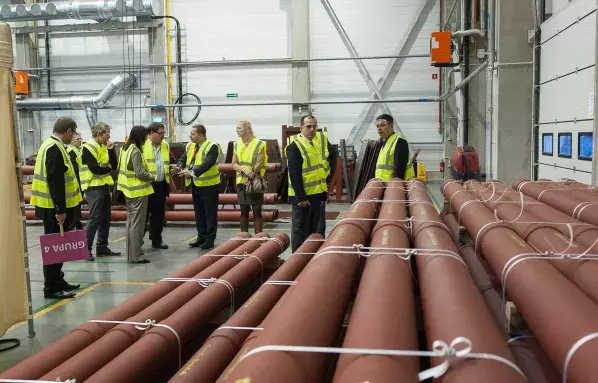
They consist of easy-to-weld mild steel tubes which have been internally wearface-welded with TeroMatec 4666 alloy, thus maintaining the exceptional wear resistance of our well known 4666 CastoDur Diamond Plates®. Furthermore, by avoiding expensive forming operations of flat plates into tubes, seamless small diameter CastoTubes® offer many advantages:
- Highly cost-effective
- Absence of harmful linear weld joints
- Exceptional wear resistance
- Perfectly round cross section
- Spiral welding minimises distortion
- Lightweight for handling
- Highest quality metal powder
- Easy-to-join by welding or mechanical means